The seemingly boundless versatility of additive manufacturing makes it an area ripe for fast evolution, but critical industrial applications also demand verification and reliability
There is no doubt that 3D printing (also known industrially as additive manufacturing; AM) has set off a true manufacturing transformation, and the chemical process industries (CPI) are among numerous industrial sectors that are benefitting from its use. From rapid delivery of spare or replacement parts to design customization, the myriad AM technologies can help streamline maintenance activities, process improvements and research. Concurrently, materials engineers are actively expanding the boundaries of printable materials to include not only plastics and metals, but also nanomaterials, bio-based substances and more. However, as 3D-printed parts make their way into more end-use applications, and more companies begin operating their own in-house 3D-printing operations, it becomes clear that standardization and inspection are crucial for ensuring safety and reliability.
Building the baseline
The unprecedented flexibility available to manufacturers with modern 3D-printing/AM technologies also introduces some sensitive issues that the industry is just beginning to understand, in terms of safety, regulatory and intellectual property (IP) ownership. To address these concerns, Penn State University (University Park, Pa.; www.psu.edu) is offering a first-of-its-kind graduate course on legal issues in additive manufacturing. "With AM, a lot of companies are trying to do spares and repairs, but one of the challenges is that these companies don't necessarily own the part or design they are trying to replicate, and they may not realize they could be in violation of someone else's IP," says Tim Simpson, director of Penn State's Additive Manufacturing & Design graduate program. In some cases, says Simpson, replicating a part can be as simple as scanning the component and generating a 3D solid model from which the part can be printed. "People aren't used to thinking about ways to protect digital copies of their part," says Simpson. He is currently part of a team of researchers developing methods to authenticate 3D-printed parts, including embedded chemical tags – essentially a "fingerprint" that can be detected with spectroscopy to provide verification of a part's provenance (Figure 1). "If you're printing a titanium part, for instance, you can print a secondary material into the part that doesn't affect properties, but can be used to verify that parts are authentic," explains Simpson.
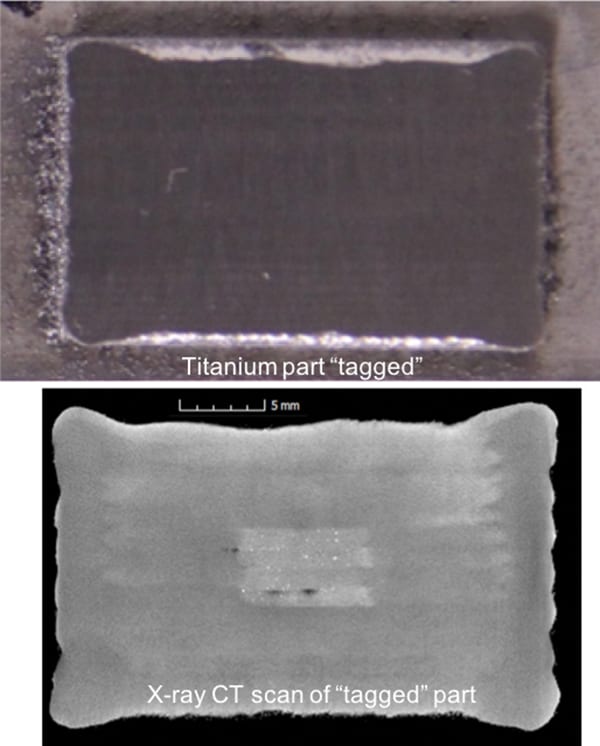
Figure 1. Chemical tags are a way to authenticate parts and protect proprietary designs Source: Penn State
Verification and standardization are also essential when considering the safety aspects of employing 3D-printed parts in critical industrial applications, but the related standards for regulated industries are not fully realized as yet, even as AM's adoption flourishes in these sectors. For example, there are currently no ASME Boiler & Pressure Vessel Codes for AM components, but work is being done to develop new rules and code cases for 3D-printed structures. However, the fast proliferation of AM technologies demands that new standards be developed and updated very quickly. "From a spares and repairs standpoint, the pressure continues to mount. People want to do this quicker than the standards bodies are ready for," emphasizes Simpson. Key to these activities is cross-industry collaboration and sharing of data, especially in demanding applications where there is cycling, fatigue or particularly high temperatures or pressures. The American National Standards Institute (ANSI; New York, N.Y.; www.ansi.org) and America Makes (Youngstown, Ohio; www.americamakes.us) have launched a standards-coordination effort to bring together relevant data for standardization of AM technologies and parts. "Rather than everyone developing standards independently that might overlap or conflict, there's some level of coordination, which hasn't really happened in the past," adds Simpson. Still, he adds, there is much work to be done, as many companies are reticent to share proprietary research or operating data, especially after spending millions of dollars to generate it.
Printed pressure vessels remain a particular area of interest, as are heat exchangers and heat sinks, but to move beyond the "spares and repairs" mindset and take full advantage of AM's capabilities, Simpson suggests that chemical processing companies should look to the new design freedoms enabled by AM. "The freedom to adapt and optimize materials – for instance, lightweighting a component with lattices – uses less material and enables viable business cases for using more expensive, longer-lasting materials. It can completely change the economics around the use case for a component."
Even with such potential for customization and process optimization, companies must continue to ensure that all parts of their facilities meet inspection requirements. "Independent verification and qualification are a way of mitigating risks and unknowns," says David Hardacre, lead specialist, Inspection Services at Lloyd's Register (LR; London, U.K.; www.lr.org). LR, in collaboration with TWI Ltd. (Cambridge, U.K.; www.twi-global.com), has developed a specific set of guidelines aimed at certifying metallic parts produced via AM, and has been certifying printing facilities since 2016. These guidelines examine many factors, including the following: feedstock receipt, storage and handling; equipment qualification; process control; personnel training; health, safety and environmental considerations; acceptance of deviations; and more. Recently, LR applied its guidelines to inspect and qualify a powder-bed fusion AM facility operated at Shell's Technology Center Amsterdam (STCA; www.shell.nl). "In 3D printing, many variables can influence the visual, chemical and mechanical properties of the printed part. This potentially introduces various risks to people, assets and the consistency of the parts produced. LR's qualification provides proof of competence in our AM processes and quality controls, thereby reducing operational risk," explains Ron van Wolferen, Emerging Technologies project manager and 3D Printing Theme Lead at Shell. Shell is developing AM projects to support assets across its entire enterprise, including seabed scans, newly shaped parts used for debottlenecking projects in hydrocarbon processing and replacements for obsolete parts (Figure 2) and research equipment, says Van Wolferen. Currently, the company is developing what is said to be the world's first 3D-printed pressure vessel. In such pioneering endeavors, says LR's Hardacre, it is important that companies strive for qualification, not only to satisfy legal and safety requirements, but also to contribute to the collaborative learning within the supply chain, which will benefit the entire industry. "As new technologies develop, standards and regulations also require development to incorporate these new ways of working to ensure that they are safe, that legal requirements are met and to provide assurance of quality and capability to end users," he continues.
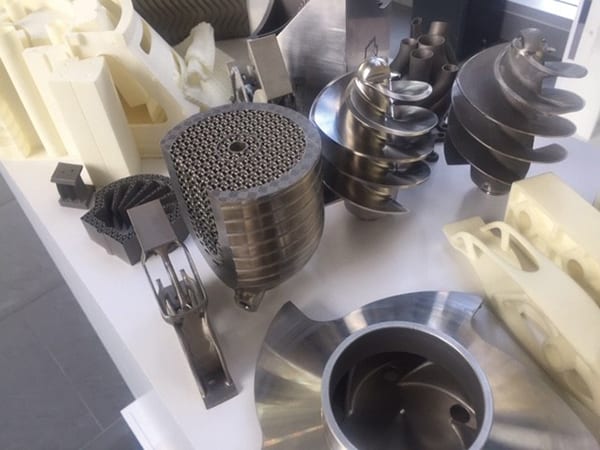
Figure 2. Shell operates a powder-bed fusion AM facility at its Technology Center Amsterdam
Source: Shell
As more groups begin to develop their own in-house printing operations, AM standards will certainly continue to evolve as the application areas expand. Currently, there is a single level of AM facility qualification, but it can be tailored to the specific AM process and materials being used within the facility, explains Hardacre. The certification requirements for printed parts may differ, depending on the risks and demands of the end-use application. "Different AM processes, different feedstocks and even different material groups impact the required testing and inspection to provide the level of confidence that the materials are fit for purpose," he adds. Moving forward, LR is contributing to several committees to further develop standards so that AM can be used safely and reliably across many industrial sectors.
Mastering new materials
One of the most exciting areas of activity is the evolution of new materials to expand the end-use applications for 3D-printed parts.
Modified steel. A research project at the Graz University of Technology (Graz, Austria; www.tugraz.at) seeks to expand the applicability of stainless-steel powders in selective laser melting (SLM) AM. In SLM, components are modeled as computer-aided design (CAD) files and then sliced into thousands of very thin cross-sectional slices, which are translated into vectors that provide a path for a laser beam to selectively melt thin layers of a metallic powder. While SLM can successfully produce complex parts, it is limited by the angle that a printed surface can be leaned. At some leaning angles (usually below 30–35 deg), SLM requires support structures, which introduce cost and complexity into the process and lengthen printing and post-processing times. These support structures must be removed – often manually – and in some specific cases, cannot be removed at all, making the part unusable, explains researcher Mateusz Skalon. Skalon has developed a method for modifying the surface of stainless-steel particles so that a component's leaned surface does not deteriorate during printing, thereby reducing the costs associated with support structures. In SLM, a rapidly moving laser melts metal particles, creating a "track" of molten metal. This melt track is extremely delicate and prone to collapse, especially at lower leaning angles. However, says Skalon, the modified steel particles are able to support the melt track so that it remains stable, even at low leaning angles (Figure 3). "The particles' surfaces are modified so they interact in a smarter way with the molten metal," he adds. Furthermore, by making steel powders more readily printed, less materials are wasted and any surplus steel powders can be recycled at the end of the process. So far, Skalon's steel modifications have focused on 316L stainless steel, but there are plans to apply the work to other steel grades as well. The modification technology currently runs at laboratory scale, and within 2–3 months, Skalon expects an industrial-scale demonstration, with commercial-ready products reaching the market in 2020. The modified steel powders are particularly applicable for topology-optimized parts, low-angle lattice structures and advanced piping and valve systems, such as those used in flow-chemistry processes.
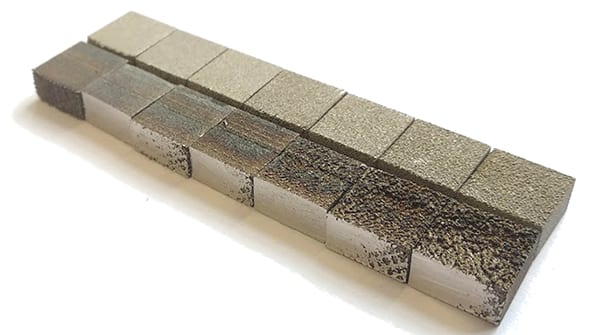
Figure 3. A new method to modify steel particles enables optimized printing with molten metal
Source: Mateusz Skalon
Diamond. Earlier this year, Sandvik Additive Manufacturing (www.additive.sandvik.com) unveiled a 3D-printed diamond nanocomposite – said to be the world's first. The 3D-printed diamond nanocomposite was created via stereolithography (SLA) using a slurry containing diamond powder and a polymer. The ability to 3D print with diamond paves the way for widespread adoption of customized, complex parts with the unrivaled hardness and other desirable properties that diamond possesses. "Being able to integrate the hardest naturally occurring material on the planet into additive manufacturing would drastically improve product properties, including increasing resilience, corrosion resistance and conductivity, as well as making parts significantly lighter," explains Anders Ohlsson, delivery manager at Sandvik Additive Manufacturing. "Furthermore," continues Ohlsson, "Sandvik's method of producing composite diamond also produces a low amount of waste because excess materials can be recycled for future use." To imbue the printed diamond part with its signature hardness, Sandvik has developed a proprietary post-processing step. "The composite is three times stiffer than steel, with heat conductivity higher than copper and a density close to aluminum," adds Ohlsson. A diverse array of industries could benefit from 3D printing with diamond, from power generation to mining to medical implants. Although the diamond nanocomposite is still in the demonstration phase, many end-use applications are currently undergoing trials, according to Ohlsson.
Graphene. A collaboration between GrapheneCA (Montreal, Que., Canada; www.grapheneca.com) and Apis Cor (Boston, Mass.; www.apis-cor.com) brings together two world-first technologies – modular, scalable graphene production and mega-scale 3D printing for construction applications – with the aim of creating an ultra-large-format 3D printing system that can handle graphene materials (Figure 4). "In 3D printing, graphene acts as a multi-tasking additive. Using graphene, you can impart a number of mechanical attributes to most materials, and it is also possible to achieve properties like conductivity, heat dispersion and controlled permeability," says David Robles, head of business development at GrapheneCA. This means that graphene can provide most of the functionality of several other additives in a single material, which leads to simpler, faster production. Additionally, explains Sergey Voskresensky, head of R&D at GrapheneCA, because graphene is chemically inert, it does not interact with glues and can act as a secondary matrix within printed media. GrapheneCA has developed mobile graphene container systems (MGCS) that can produce four tons per month of dry-weight graphene using a straightforward water-exfoliation process.
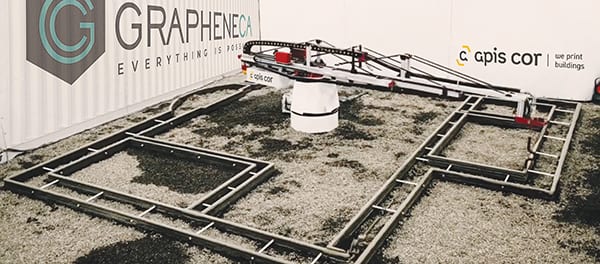
Figure 4. Incorporating graphene materials into mega-scale 3D printing involves the development of specialized nozzles and mixing systems Source: GrapheneCA
GrapheneCA's team is currently designing a specialized mixer and extruder system, along with new printer heads, for graphene compatibility with Apis Cor's newest 3D printer. For 3D-printing applications, mixing is especially crucial, because graphene has the tendency to settle into low-viscosity media and an even dispersion must be maintained. However, GrapheneCA has addressed these concerns with its graphene-geopolymer composites, in which the graphene is mixed and made, and can be produced on location, alleviating settling and agglomeration issues with aqueous inks.
Apis Cor's modular printing systems are tailored for very large construction projects, including barges, warehouses, pipelines, storage tanks and more. "This is one of the only 3D printers of its size that isn't stationary," says Robles. The printing capacity is around 2,500 ft 2 of material in 24 hours, for structures up to 20 ft tall. The ability to incorporate graphene-based materials into these printers will expand the application areas, as well as the robustness of final printed structures, such as printed buildings that can withstand extreme weather conditions. "Right now, we are looking into how to make locally producible inks for the printer and new nozzles that will make these printers an ideal building solution," adds Voskresensky. "Our process equals a high-quality, longer-lasting build that requires less labor and materials."
More materials innovations. Some highlights of additional innovative projects in the area of 3D-printing materials are summarized below:
- Oak Ridge National Laboratory (Oak Ridge, Tenn.; www.ornl.gov) has developed a patent-pending renewable composite of lignin and nylon for 3D printing
- HRL Laboratories, LLC (Malibu, Calif.; www.hrl.com) is commercializing a high-strength aluminum powder for 3D printing and has become the first organization to be granted an alloy registration number for an AM material by the Aluminum Association (Figure 5)
- Evonik Industries AG (Essen, Germany; www.evonik.com) developed the industry's first 3D-printing polymer filament based on PEEK (polyether ether ketone) that is suitable for use in medical implants (Figure 6)
- Clariant AG (Muttenz, Switzerland; www.clariant.com) offers glass-fiber-filled, flame-retardant polyamide 6 3D-printing filament materials that meet UL 94 Flammability Safety Standards
- Wacker Chemie AG (Munich, Germany; www.wacker.com) has developed a proprietary 3D-printing process specifically for silicone rubbers. The newest version can print up to four different silicone materials simultaneously
- Late last year, Arkema (Colombes, France; www.arkema.com) introduced a new polyetherketoneketone (PEKK) masterbatch with multi-wall carbon nanotubes for filament printing applications
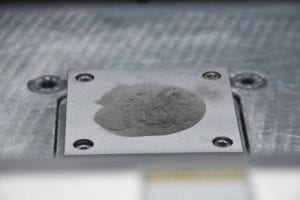
Figure 5. HRL's new high-strength aluminum alloy is designed specifically for additive manufacturing Source: HRL
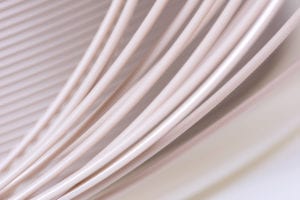
Figure 6. The world's first polymer filament based on PEEK (polyether ether ketone) for use as a 3D printing material for implants Source: Evonik
CPI investment spurs innovation
The advantages of AM to the CPI are multifaceted – in many cases, the companies that benefit from rapid manufacture of spare or customized parts may also themselves produce advanced materials that can be used in AM processes. This synergy has spurred significant collaboration.
For instance, BASF SE (Ludwigshafen, Germany; www.basf.com) recently invested in China-based AM technology provider Prismlab, with the aim of tackling new 3D-printing applications, particularly in areas where mass production and precise materials specifications are required. Prismlab has developed a SLA-based 3D-printing process known as Pixel Resolution Enhanced Technology wherein a pixel is divided into several parts. These parts are individually cured via exposure to an LCD light, resulting in higher energy input into each pixel, and ultimately, higher printing resolution without printing speed losses. This yields hardened parts that are more stable and homogenous, enabling larger parts to be printed than with conventional SLA processes, and even for multiple components to be printed in a single step. Furthermore, the use of an LCD light source rather than a laser reduces equipment and energy costs. Prismlab uses an LCD light source that allows printing on the surface level, which significantly increases the total output, says BASF.
In July, Covestro AG (Leverkusen, Germany; www.covestro.com) announced a partnership with Carbon, Inc. (Redwood City, Calif.; www.carbon3d.com), the developer of the ultra-fast AM method known as Digital Light Synthesis (DLS). DLS is said to produce parts up to 100 times faster than typical SLA processes. Covestro is researching materials to complement DLS and aiding in scaleup of DLS for mass production. Similar to other AM methods, DLS begins with a liquid resin that is cured with ultraviolet light. The resin is contained within a vessel whose bottom is a light- and air-permeable membrane through which oxygen is supplied to counteract the curing, creating a functional dead zone and enabling the printed part to be continuously pulled upward. This results in high levels of consistency in all directions and enables DLS to effectively utilize a wide swath of materials.
At the 2019 RAPID + TCT conference, Dow Chemical (Midland, Mich.; www.dow.com) joined forces with AM specialists German RepRap GmbH (Feldkirchen, Germany; www.germanreprap.com) and RDAbbott (Cerritos, Calif.; www.rdabbott.com) to demonstrate the capabilities of liquid additive manufacturing (LAM) with liquid silicone rubber. GermanRepRap has developed the world's first production-ready LAM printer. LAM with silicone enables printing of complex geometric shapes, including lattice and honeycomb structures.
Earlier this year, Evonik and Evolve Additive Solutions Inc. (Minnetonka, Minn.; www.evolveadditive.com) partnered to develop polyamide materials for use with Evolve's proprietary AM technology, selective thermoplastic electrophotographic process (STEP). The STEP process is expected to reach commercialization in late 2020.
Henkel AG & Co. KGaA (Dusseldorf, Germany; www.henkel.com) has joined a German-Austrian consortium known as SYMPA aimed at advancing materials and applications for SLA products using Digital Light Processing (DLP).