The chemical process industries (CPI) are in the midst of a profound evolution, and technological changes – especially those in the digital sphere – are being implemented at an accelerated pace.
Simply put, digitalization is the leveraging of digital technologies to transform an existing or proposed process setup into a digital framework. Energy management is one area poised to greatly benefit from cutting-edge digital technologies.
Along with key aspects related to general digitalization, this article describes how organizations can improve their production and energy efficiencies by using digital tools and techniques, and also includes vital inputs from industry experts.
The market is flooded with tools to reduce and control energy intensity. However, many large organizations are still reluctant to invest in such capabilities. At times, this reluctance is due to the lack of knowledge and awareness of the best suitable tools, while some cite budgetary constraints and others veer away due to lack of management focus and enthusiasm (possibly due to lack of clarity regarding expected returns on investment). Even with powerful tools at their disposal, many corporations may still question why to digitalize when they already have an established setup. The benefits are multifaceted, including the following:
- Easing general system burdens
- Making processes more systematic
- Making useful insights easier to retrieve and comprehend
- Streamlining resource optimization and analyses
- Improving stability and efficiency
For these reasons, digitalization is increasingly becoming ubiquitous and successfully adopted in many spheres of life, from the manufacturing sector to transportation, healthcare and even government entities.
Laying the technological foundation
The proliferation of digital technologies is highlighted by the International Energy Agency (IEA; Paris, France) in its Energy Efficiency 2019 report, which shows that that between 2015 and 2018, growth in digital activity outpaced both population and economic growth. The number of digital devices globally increased from 15.5 billion to 20 billion. This growth, of around 8% per year, was much higher than population growth (1.1%) or economic growth (3.5%). IEA further highlights that the global primary energy intensity (an indicator of energy used by the global economy) improved by just 1.2%, the slowest rate since 2010.
Many in the CPI are already reinventing and restructuring growth strategies, including the use of high-end, digital, value-added services to supplement existing product offerings. Various digital platforms that have become prevalent in the CPI are shown in Figure 1.
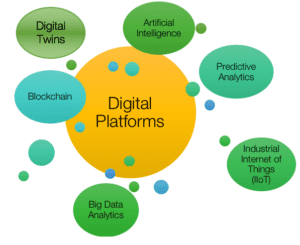
Figure 1. There are numerous interconnected digital technologies that are contributing to the CPI's digitalization journey
Digital twins: As industries are now moving from steady-state to dynamic process optimization and control, a critical tool is the digital twin, a real-time dynamic model that runs parallel to an operating plant. This dynamic model populates data from devices installed in the plant to match the plant's realtime status and operating condition and accordingly carries out offline dynamic studies for optimizing plant performance.
Smart sensors: Thanks to the wide variety of smart sensors, and their capabilities to continuously measure process values, record data and trigger alarms, it is easier than ever for engineers to plan ahead and take timely corrective actions. In turn, these capabilities also save energy by enabling online process improvements and better-planned machine overhauls and preventing sudden outages.
Process simulation: With emphasis on cost optimization and tightening environmental standards, many CPI companies have deployed advanced process simulators in applications ranging from pilot-scale and laboratory trials to large-scale commercial processes. Besides offering training, these simulators provide realtime data for predicting performance and optimization. In some cases, process licensors have collaborated with simulation developers and now offer a comprehensive package during the commissioning of new plants. These packages validate and reconcile data, enable virtual sensing and offer predictive control.
Before embarking on a digitalization journey with such advanced tools, it is important to consider the "ABCDs" of digitalization, and the ways that human interactions form the foundation for an effective digital transformation.
Agility: This feature of digitalization must be present in both the human mindset and the process being digitalized. If employees are not ready to adapt, then digitalization fails. By nature, the human mind resists change – employees may look for bypasses or open loops and often attempt to trick the system. The workforce must also digitalize alongside processes.
Better connectivity: Connectivity issues and IT-related hiccups must be dealt with before starting any digitalization project. If such issues are not addressed in the incipient stage, the entire digitalization process collapses.
Communication network: Another key component is communication, which must not be undermined. If the process lags in communication capabilities, employees may be unable to take appropriate and corrective action to complete their digitalization tasks.
Data analysis: A digital process is fast-paced and it processes massive volumes of data very quickly. The presentation of this data should ensure that useful data is quickly populated, easily accessible for rapid analysis. However, even if the data is represented in a user-friendly manner, employees may still remain reluctant and passive, so human behavior is actually an important focal point in the data-analysis pillar. Therefore, it is imperative that the data component be preceded by some sort of formal training to increase employees' acceptance and understanding of the necessary human-machine interfaces (HMIs).
Case study
Consider an ammonia plant that installed an advanced process control (APC) system. The aim of the APC implementation was to check energy intensity, reduce standard deviations of the key operating variables, maintain product quality within certain specifications and maximize throughput. This ammonia plant may primarily be divided into a front-end section (reforming, CO2 removal and shift converters) and a back-end section (synthesis loop and refrigeration). The APC covered the critical plant loops and parameters. Figure 2 illustrates the plant's reformer loop.
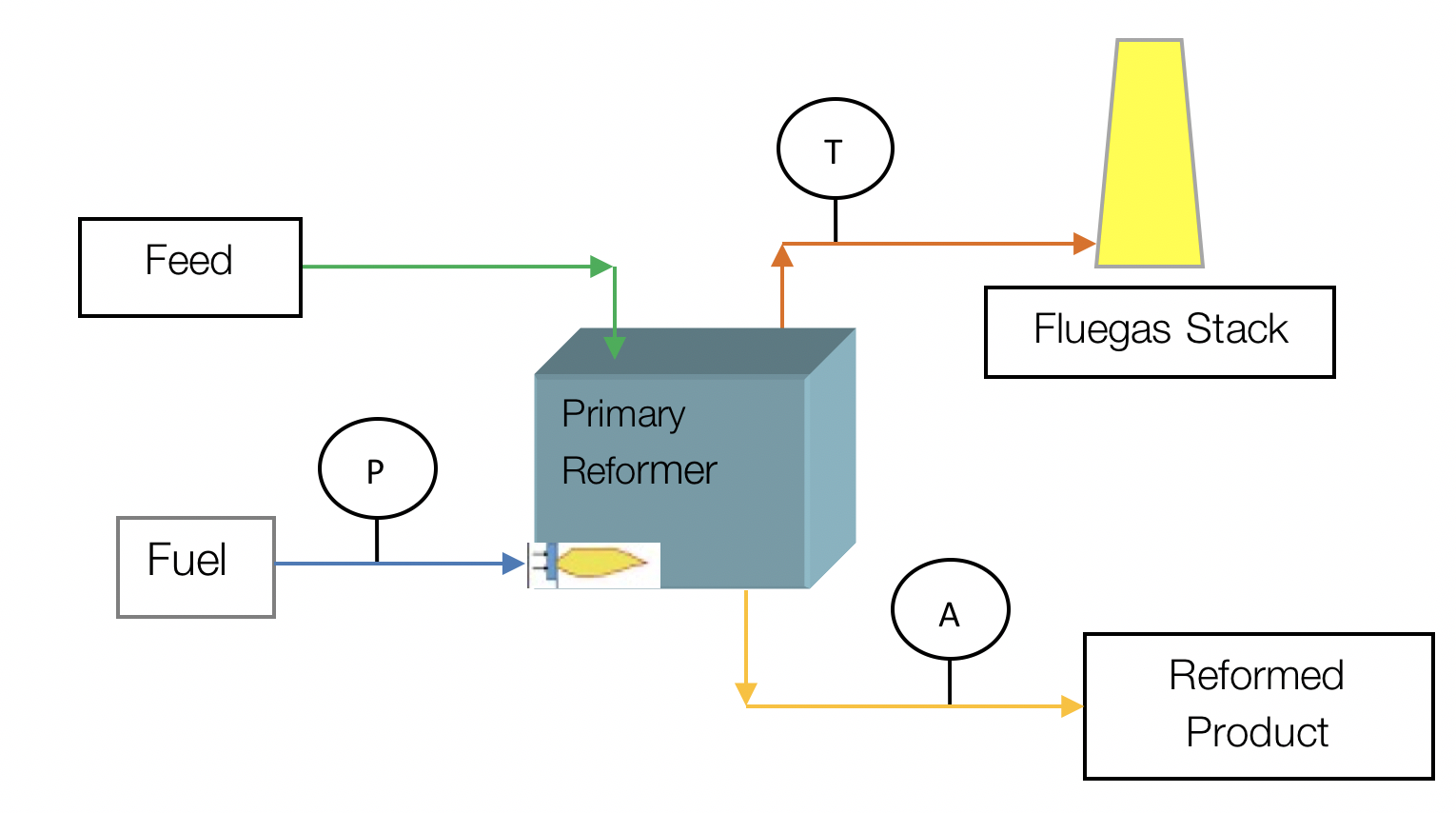
Figure 2. The reformer loop in an ammonia plant, which is controlled via an APC setup with optional manual-control mode
As shown in Figure 3, a multivariable optimizing controller (MOC) was used for the entire ammonia plant. These MOCs have sub-controllers for different sections. This example will focus on the primary reforming fuel (Subcontroller-1) loop and will explain the algorithm developed and its function. In this sub-controller loop, the primary reformer fuel pressure-control valve is automatically manipulated, keeping an eye on controlled variables like reformer outlet temperature, methane slippage and fluegas temperature. Amongst them, fuel pressure and fluegas temperature serve as constraint variables. This means that when fuel is increased or decreased, it looks upon both the pressure-regulating valve output and the fluegas temperature before manipulating the controlled variables. It cannot breach its defined range unless a human intervenes.
When all the conditions are satisfied, the APC switches to the optimization mode, where it aims to optimize reformer energy. The system, upon sensing deviations, is capable of exiting APC-controlled mode and transferring to human-controlled mode during plant upsets. This setup enables reformer fuel to be regulated without human intervention, thus optimizing plant energy consumption.
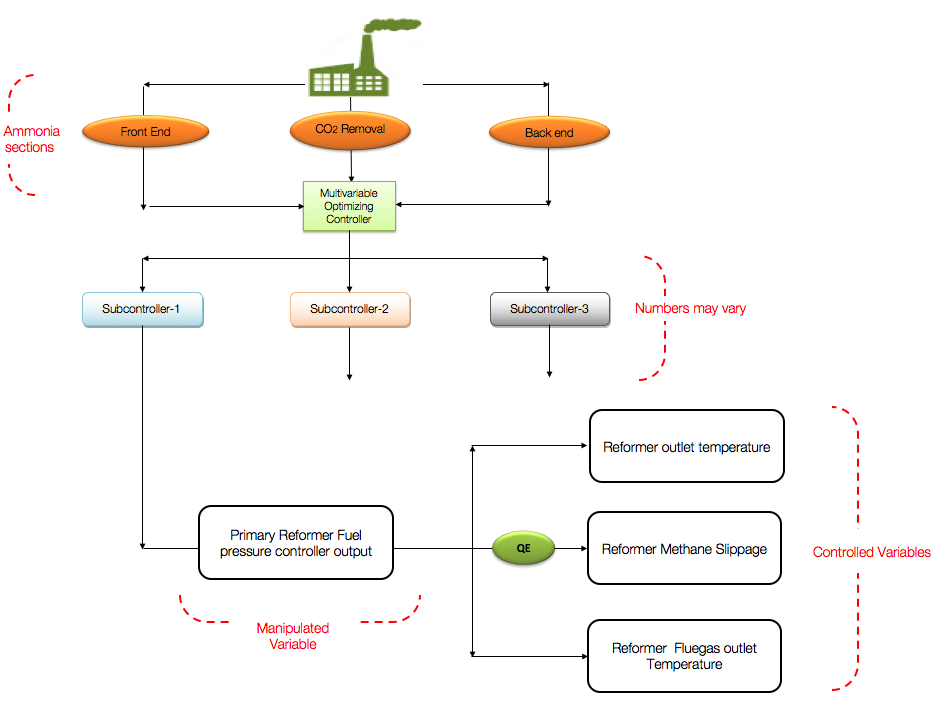
Figure 3. The algorithm applied to the reformer's APC loop enabled optimized operation, with manual intervention only required during process upsets
Overcoming challenges
For the CPI to reap the benefits of plunging into the digital world, it must first overcome the challenges digitalization presents and treat them as prerequisites for customization and effective utilization.
Rigidity in structure: Many organizational structures in the CPI are very rigid, and companies often take pride in streamlining operations. This trend now has slightly subsided thanks to confidence built up by robust sensors used for data generation. Before leaping into digitalization, a cultural shift and readiness amongst its users should be developed.
Lack of convergence: Although it is often considered as such, digital change cannot be just the prerogative of information technology (IT) departments. Due to ownership uncertainty, friction between the IT team, the engineering team and the end user can occur, which hampers the seamless integration of the entire process setup. Data scientists, technology facilitators and the end users must join together to define ownership roles.
Cyber insecurity: With cyber-breaches occurring on an unprecedented scale, overcoming of cybersecurity risks can seem like an intimidating task. In this regard, confidence and trust-building measures, as well as reference examples of digitalization success stories will go a long way in allaying this fear.
Long lead times: The lead and commissioning times to integrate digitalization into a process setup can be very high. With the process industries already stressed to reduce downtime, it becomes all the more imperative that digital service providers think of innovative ways to reduce the installation time. At the onset, it may be useful to constitute a committee to take the lead in scaling up digitalization activity.
Failure to understand the process: In addition to advanced competency in digital technologies, the team carrying out the digitalization projects must also understand the chemical process itself. It may be useful for the process specialists to provide training for the digital implementation team to share a brief primer on the specific process chemistry and any other necessary technology parameters.
Lack of standard approach: Although much has been said about the advantages of holistic digitalization across industry verticals, there are, so far, few or no industry-wide standardized procedures to which the CPI can refer. To overcome this, a standard framework is needed to help the industry to reach the intended destination on the digital journey.
Improving efficiency
Digitalization outreach is not just limited to assimilating datasets and putting them in concerted and easy-to-comprehend forms. Digitalization also boosts productivity by checking and predicting untimely process incidents, equipment failures, instrument malfunction and non-redundancy, culminating into increased on-stream hours. Digitalization, with its power to portray realtime data and their subsequent impact, also has capabilities to highlight and rectify potentially unsafe conditions. Furthermore, decreasing plant outages means that plants can avoid gas blowdowns and stack venting, which will result in overall lower atmospheric emission levels. By cutting short unproductive hours, digitalization thus results in better environmental performance.
Digitalization has drawn parallels and gradually moved the CPI's workforce from intuition-based decision-making approaches to results-oriented and, ultimately, more organized approaches. With digitalization strategies in place, employees can feel more empowered to face process incidents. This empowerment boosts confidence and enhances overall reliability.
Additionally, with sound digitalization strategies in place, an organization's decision-makers may find it relatively easier to budget and plan annual maintenance programs. The energy and site management policies can be framed accordingly, aligning all employees toward a common company vision and culture.
With the world's growing aspirations for a sustainable and reliable future, industries must prioritize digitalization to help rein in energy and resource consumption. Digitalization is certainly an investment which, when coupled with the right mix of management intent, can make great strides in optimizing energy usage. Though many digital technologies are now well established in the CPI, many challenges will still arise, including evolving government regulations, increased competition, volatile markets, ever-changing customer demands and dynamic cost equations. Today, more than ever before, companies must innovate and digitalize, not just to survive, but thrive in the future.
Insights from industry
To further underline the industry's shift toward all things digital, experts from around the CPI provide their thoughts on digitalization's trends and future outlook.
Mark Brouwer, owner and director, Urea KnowHow: "Digitalization can play a key role in improved practices in the design, fabrication, construction, operation and maintenance of CPI plants. The safety and reliability of the CPI depends greatly on assuring the integrity of high-pressure equipment, piping, accessories and pumps. Digitalization supports improved quality and quicker procurement activities, better communication between all parties involved in designing, constructing, operating and maintaining plants and opens the door to co-operate efficiently from remote locations. It supports operating the plant at optimum process conditions and facilitates in continuous monitoring of critical equipment and instruments."
Rajan Desai, secretary of the Heat Transfer Society of India (HTSI). "Before the pandemic, we were seeing an increasing interest in the use of digital twins in the CPI. Now, this year, there has been an explosion in growth and interest. The adoption of Internet of Things (IoT) and big data analytics across the industry has further contributed to the rise of digitalization. Leading processors have already integrated digitalization solutions in their assets, mainly for better monitoring and optimized usages – more precisely to make the existing assets more competitive and operations more reliable, safe and energy-optimized."
Jason Shirley, managing director ECP Energy & Chemical Professionals UAE. "Digitalization as the game changer with its ability to provide data continually. The immediate advantages may be efficiency improvements, increased uptime and improved safety and reliability. However, with distributed aging assets in process industries, digitalization poses herculean task and throw altogether different challenges."
Karthikeyan Balan, process safety consultant. "Digitalization is a major area of interest and has its own pros and cons. One must remember the bigger picture always and exercise caution while implementing. We must not forget the human element in the midst of digitalization. How will the human use it? Digitalization, on one hand makes data collection and presentation very easy, and helps to improve processes, but it's ultimately the human that makes the decision."
Dan Cojocaru, director Fertilizer Industrial Service Ltd., UK. "Before embarking on digitalization process, an organization should question themselves first about whether they are ready from a human-resources perspective to implement digitalization and if their plant is capable to support and accommodate the digitalization technology. Some old facilities may require significant modifications and investment to accommodate digitalization. One might find out that an old setup is not suitable for digitalization. However, for greenfield projects, digitalization is comparatively easier and may be implemented from the beginning itself." ♦
Edited by Mary Page Bailey
Author
Rohit Shukla is a process manager at Chambal Fertilisers and Chemicals Ltd. in Kota, Rajasthan, India (Email: rohit.shukla@chambal.in). He holds an Industrial Safety certification from the National Productivity Council, India, and is also a Certified Energy Manager (CEM), as designated by the Bureau of Energy Efficiency. He is responsible for Process Safety Management (PSM) at Chambal.