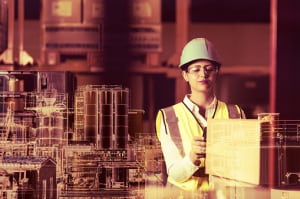
Engineers can apply new technologies for machine learning and data analytics to streamline maintenance and improve operational excellence
New digital capabilities have enabled a revolution in the way process equipment maintenance can be approached, but the true impact of these newfound insights depends on organizational collaboration
The chemical process industries (CPI) are facing a new economic landscape with pressures that are forcing companies to find new efficiencies and cost savings in every pocket of production and operations. While new efficiencies are hard to come by, there exists a new frontier for improving operations in maintenance and reliability: asset performance management. No longer is maintenance simply preventative work. Leveraging realtime data and rich process knowledge and incorporating advanced analytics into maintenance can drive greater prescriptive capabilities, reliability, performance and uptime. However, a willingness from companies to strategize around the concept of asset optimization is required to make this digital transition a reality.
Moving forward will require the adoption of more scientific approaches and strategies when it comes to asset optimization, parting ways with the old-school thinking of just performing consistent, scheduled maintenance. Modern strategies look beyond basic maintenance, to monitor signals in realtime and impart immediate recommendations and insights about the overall health of an asset and its impact on the larger system in which it works.
The CPI must stop viewing maintenance as something that is unpredictable or unmanageable. Quite the opposite is true. With the right combination of data science and machine learning, precursors for asset failure can be modeled, leading to recommendations and insights months in advance of breakdowns. Those recommendations might pertain to operational changes or actions required for a specific asset or suggested timing around that action to ensure the highest chance at optimizing the performance of a particular asset or system. It is a granular and advanced approach to maintenance that can not only protect against unexpected downtime, but also help to optimize performance.
Market realities set stage for asset optimization
No matter how efficient a process is – be it through design or operational excellence – outside demand for products, costs, external pressures and market volatility create unexpected burdens and pose a constant threat to success. For years, the concept of operational excellence helped the CPI maintain profitability. In economic booms, it helped companies scale their businesses. In economic busts, it helped cut down on production costs. Now, however, with a new landscape putting additional pressure on these companies, operational excellence is more important than ever. To achieve the highest levels of operational excellence, businesses must adopt new strategies for asset optimization to make sure they are able to meet expectations and rise to market challenges. Asset optimization, at its core, means preventing unplanned downtime and increasing the effectiveness of the assets that work to produce profitable outcomes, cutting costs in the overall workflow. In the past, maintenance was always viewed as a creator of costs rather than a value-added activity. However, when digitized, maintenance can lead to a more universal asset-reliability program that can have a direct impact on capital-cost reductions and overall cash flow. Improved asset maintenance is truly a new frontier for additional profitability in capital-intensive environments.
The science of maintenance
When people think of maintenance, they may associate it with words like unprepared, unplanned and unavoidable. Asset optimization maintenance is an entirely different entity from traditional maintenance practices. As technology advances, the science of maintenance has emerged. As it happens, 82% of all failures cannot be avoided with traditional condition-based maintenance tools and monitoring equipment, according to ARC Advisory Group (Dedham, Mass.; www.arcweb.com). Additionally, scheduled maintenance alone will not fix or avoid all breakdowns. It certainly will not ensure asset optimization. Furthermore, one company reported that 85% of equipment failed on a random basis no matter how much the assets were serviced and inspected. This is what happens when plants depend on conventional methods for maintaining asset performance that rely on models based on rules engines, equations and statistical methods.
Advancements in technology (a combination of data science and modeling) have enabled the industry to rethink the value of maintenance and turn it into a true science. Through powerful sensors, data science and machine learning, companies have the ability to realize sustained value throughout the entire plant lifecycle and to continue scaling and growing. New technologies can use historical and realtime data to predict the origin and cause of asset failures and recommend the actions and next steps required for operators to avoid future failure. This approach sets a baseline for the effectiveness of all assets through insights gleaned.
This process involves a combination of complex digital interactions at many different levels. Machine learning technology absorbs sensor and maintenance data over long periods of time and then identifies patterns in that data – patterns that would typically remain elusive to an operator. A major benefit of machine learning is that it can learn under all different types of conditions (for instance, seasonally, different operating campaigns, varying duty cycles and more) based on the real-world behavior of the equipment. It measures learned failure signatures from a machine, as opposed to modeling machine environments. Those learned signatures can then transfer from one machine to another similar machine to help that machine avoid the conditions that caused failure in the initial machine. Machine learning technology also then presents actionable results (reliability) and recommendations in realtime, protecting hundreds of thousands of unique assets – something not achievable with traditional condition-based modeling.
Modeling is still important, though, as the right combination of plant- and site-level modeling paired with asset analytics can aid in operational decision-making, helping to identify the most vulnerable assets and specific causal effects and conditions of those assets within a plant. This helps to create an overarching view and analysis of the key processes and performance of every asset, enabling engineers and operators to act far in advance of any failure of large assets or larger systems in which those assets operate. This epitomizes a new strategy for maintenance and optimization that coordinates all the different signals and the understanding of how asset operation impacts system-wide performance, using machine learning, cloud computing and advancements in software and analytics. Machine learning can process enormous data sets and provide recommendations based on that data. The cloud allows for the data to scale, bringing realtime insights – which are imperative in avoiding failures. Software sets the stage for a full integration of all the technologies and different types of data, safeguarding optimal production and reliability. Having advance warning and recommendations gives engineers the ability to take time to scope out alternative measures or strategize around different approaches that will yield better outcomes, making maintenance more like a straightforward science.
Driving asset reliability
Modern asset-reliability strategies can help to realize additional cost savings and optimize the entire lifecycle of a plant. They also help companies avert the risk of a plant shutdown or failure. The shutdown of a plant or a portion of a plant for just one day can result in considerable lost profit – sometimes a year's worth of productivity, not to mention costs associated with equipment damage and equipment replacement.
These strategies make it possible to identify specific assets or parts of a system that are at risk of breakdown months in advance of failure actually occurring, salvaging both productivity and the actual asset. This also allows assets to achieve the same operational excellence that design and operations have achieved before it. The idea of this type of reliability is in stark contrast to the current maintenance environment, where operators have no forewarning at all or receive notifications (sometimes with false alerts) no more than a couple of days in advance. In that kind of scenario, there are not many actions that can be realistically taken to prevent failure, especially if the failure identified is in a remote location with no maintenance engineering crews on site. These advances in asset management and reliability mark a new way for the CPI to maximize additional efficiency and reliability after design and operations optimization have taken place. So many companies are currently spending large sums on maintenance, despite the constant potential for shutdowns and lost revenue. Relying on models that focus on the asset itself, rather than the on signals the asset generates, is a risky approach in this economic environment and with the uncertain patterns of supply and demand of every capital-intensive industry.
Agents of change in the digital transformation
While digital transformation opens the door for the CPI to achieve unmatched efficiencies and results, the technology itself is not what initiates change. Change only occurs if organizations redefine the backbone of their cultures, incorporating technology and pushing employees themselves to be agents of change. Organizations must break down silos and nurture a problem-solving mentality in their employees. They must work to make sure employees know how to use these technologies and how these technologies reshape their working relationships with their colleagues, other departments within their company and their own, personal responsibilities. When thinking about giving these new asset-management concepts a foothold within a company, the following lean manufacturing principles offer an effective guide for how to introduce a cultural attitude around the technological applications, specifically for maintenance and operations teams.
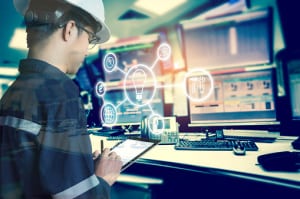
A collaborative team will help to break down data silos and ensure that organizations can work toward new frontiers in maintenance efficiency
First, teams must do a deep dive into their performance and check to see the current status of their reliability goals. There needs to be a universal understanding that just because something is performing well, does not necessarily mean that it is performing at the very best of its abilities. Then, it is important for teams to assess – together – where problems occur in the overall process. This enables teams to work in tandem to develop solutions. Organizations should also reward individuals for new ideas or small improvements in the process – data and analytics-based insights can only take an organization so far. There must be individuals acting on the insights and making smart decisions based on the data. Finally, collaboration and teamwork are imperative to realizing success. Every department and unit plays some role in asset optimization, so it is critical that respect and empathy for others serve as leading and guiding values in any organization.
Taking action now
The time is now to start implementing new strategies to evolve maintenance functions. Technologies and data analytics are readily available to support this quest for the last frontier of operational gains – one that will yield greater output and less downtime. It is invaluable for companies to begin thinking about their asset optimization approach and how to best strategize around introducing it to staff. ♦
Edited by Mary Page Bailey
For more information about advanced asset-maintenance strategies, please read Rotating Machines: Digital Technologies to Enable Predictive Maintenance (Chem. Eng., March 2018, pp. 32–37).Author
Robert Golightly is senior manager, Asset Performance Management (APM) product marketing at Aspen Technology Inc. (2500 CityWest Blvd., Suite 1600, Houston, TX 77042; Phone: 281-584-1000). Prior to his current role, Golightly managed the product marketing function for the company's advanced process control (APC) and Manufacturing Execution Systems (MES) product lines. Robert's professional background includes work for SaaS provider FineTooth, as well as Pavilion Technologies. He holds a degree from Texas Tech University.