An overview of how the chemical process industries are looking to the IIoT to help form new business models in a competitive environment
Today, technological advances are being made and implemented at an accelerated pace that is quickly changing the way we live and work. In our day-to-day environments we encounter "smart" objects, including our phones, cars and devices throughout our homes. And, these devices are being connected to each other. This trend is also taking place in industry, and while perhaps not as rapidly as with our personal devices, changes are occurring quickly.
What is the digital transformation?
More and more, smart sensors and equipment that contain smart diagnostic features are being used in industry to generate large volumes of data. Advanced computing technologies are allowing these devices to be connected to each other, and to use the data in a variety of ways. This growing interconnectedness of industrial operations is what is meant by the now familiar term, the Industrial Internet of Things (IIoT). As Marcelo Carugo, senior director Chemical and Refining Solutions, Emerson Automation Solutions (St. Louis, Mo.; www.emerson.com) states, "IIoT is partly about how we make data accessible and then get the right data to the right person, in the right format, at the right time – to make a decision. It's about transferring digital data into digital intelligence by using the thousands of touch and sensing points in your plant and advanced analytics to help you recognize patterns and make decisions based on patterns instead of individual measurements."
Industry 4.0 is another familiar term, perhaps more so in Europe than elsewhere, because it has its origins in Germany. The term refers to this interconnectedness and related concepts in the digital transformation as a fourth industrial revolution, with the first three including mechanization, mass production and automation. Digitization, digitalization and "smart industry" are additional terms associated with the current movement toward the implementation of IIoT and the newest digital technologies. These terms are used interchangeably by some, and defined more rigorously by others, but in general they all refer to the same trend that goes beyond connecting things, and often refers, in a broader sense, to connecting the process to the business as well (Figure 1).
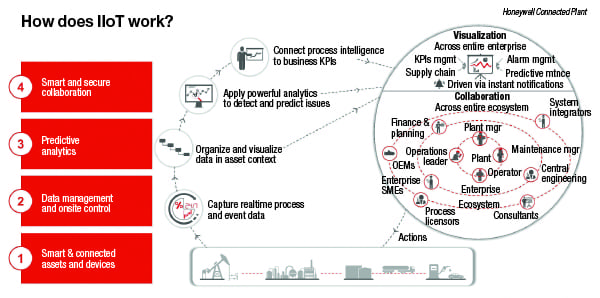
Figure 1. The Industrial Internet of Things (IIoT) can connect assets across a company to create a powerful interconnected enterprise as depicted in this graphic
Advances in sensors, data analytics, computing networks (the "cloud"), software, additive manufacturing, unmanned aerial vehicles (UAVs or drones) and more, are enabling this fourth industrial revolution. While the chemical process industries (CPI) may be slower to adopt some of these technologies than the consumer market, the CPI are very familiar with the use of sensors and automation and are well poised to take advantage of the newer technologies. As Billy Bardin, Global Operations Technology Center director for The Dow Chemical Company (Midland, Michigan; www.dow.com) states, "In general, the process industries have been slower to adopt these new technologies than the consumer and service sectors, but the process industries do have an advantage with the installed instrumentation base that has been a mainstay of our technology for decades. We have significant amounts of data from our instrumentation and process sensors to use with the new analytics and deep-learning technologies."
Insights from industry leaders
A key driver for the digital transformation in the CPI is maintaining a competitive edge. Global competition, immediate communications and technological advances are creating an environment where businesses need to respond with increasing speed. Aligning production and business through the tools available with digitalization offers new possibilities for business models.
John Cate, commercial director for Surface Chemistry at Akzo Nobel N.V. (Amsterdam, the Netherlands; www.akzonobel.com) says, "We've been driving digitalization across our entire business. It's all about efficiency and optimization. The digital world delivers more comprehensible and actionable data than we have ever had before. By replacing gut-feeling with comprehensive, realtime data, we are able to make better decisions. Whether this is about plant utilization, selecting R&D projects to fund, or sales accounts to focus on, we now have data work for us instead of the other way around." He further explains that IIoT can help combine supply and demand intelligence and that it is essential in today's environment, "Forget about getting ahead – just to ensure survival in today's chemical industry, this [IIoT] should be high up on top management's agenda. And the earlier you start understanding the IIoT and implementing digitalization, the more effective you'll be in execution over time."
Dow's Bardin also expects digitalization to affect all aspects of business and production. "We are connecting data streams from R&D, marketing, supply chain and manufacturing to better serve our markets," he says. And he also sees applications in safety and sustainability, "We can use robotics, augmented reality, big data, the digital twins and other aspects of Industry 4.0 to help achieve Dow's 2025 sustainability goals and to continue to improve our safety performance. Safety, as well as cybersecurity, remain paramount as our industry continues to evolve."
Earlier this year, Evonik Industries AG (Essen, Germany; www.evonik.com) confirmed its commitment to the digital transformation by establishing a digitalization subsidiary, Evonik Digital GmbH (Figure 2). The group is building digital expertise and developing digital business models under the guidance of Henrik Hahn, who holds the newly created position of chief digital officer (CDO). Evonik is also the first chemical company to join the Industrial Internet Consortium (IIC; www.iiconsortium.com), which is a global organization formed to promote the growth of the IIoT. Hahn says that it will become more and more common to realize truly personalized customer experiences, and in the future, there may be more competition between business models rather than between products or process technology. "Therefore we believe strategy, not technology, drives digital transformation," he says.
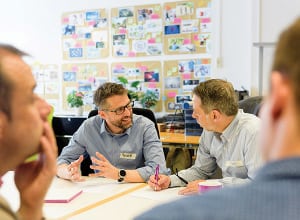
Figure 2. Rainer Gimbel (left) and Jeff Landau (right) are digital strategists in Evonik's newly formed digitalization subsidiary, Evonik Digital GmbH
Technological advances
Technology, however, is an enabler for digital transformation. There is much going on in this area, and new developments are occurring quickly. Several key developing areas are the following:
Sensors have been ubiquitous in the CPI for decades. In recent years, however, advances in smart sensor technology and implementation have helped to make sensors one of the powerful enablers of the IIoT. Automation vendors, such as Siemens AG (Munich, Germany; www.siemens.com), Endress+Hauser (Greenwood, Ind.; www.us.endress.com), Honeywell Process Solutions (HPS; Houston; www.honeywellprocess.com), Emerson and many others offer a wide variety of sensors. Regarding sensors, Jeroen Pul, marketing manager and digital lead for AkzoNobel Surface Chemistry says, "More sensors equals more data. More data equals better decisions. In general, and at AkzoNobel, we're employing more creative use of sensors to measure all aspects that impact our business."
In addition to developing new sensors, research is also going on to optimize placement of sensors – where do you best locate them in a plant? Stephen E. Zitney, at the Research & Innovation Center, U.S. Dept. of Energy, National Energy Technology Laboratory (NETL; www.netl.doe.gov) is studying underlying technologies for optimal sensor network design in a digitalization framework. Four key applications for optimization-based sensor placement technology include: better disturbance rejection in plants; better state estimation (using data from other sensors to estimate process variables that are not directly measurable, perhaps due to harsh operating environments); condition monitoring (the "health" of equipment); and fault diagnosis.
Augmented and virtual reality are familiar to some from the gaming industry. Advances in virtual reality software and more readily available hardware are enabling the use of these techniques in the CPI. Two of the targeted application areas are training and asset management.
One example of a dynamic simulator enhanced by a 3-D virtual plant is one that was developed and deployed at the Advanced Virtual Energy Simulation Training and Research (AVESTAR) Center at West Virginia University (Morgantown; www.wvu.edu) in collaboration with the NETL. The simulator is for an IGCC (integrated gasification combined cycle) system with carbon dioxide capture (Figure 3). NETL's Zitney, who led the project, explains that it provides a very realistic, immersive training system for operators, engineers and students. It is currently being used at the university to educate chemical engineering students in process dynamics, operations and control. Vendors, such as Schneider Electric (Rueil-Malmaison, France; www.schneider-electric.com) and others, offer software for augmented and virtual reality simulations.
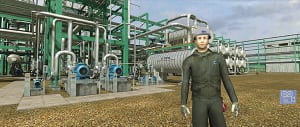
Figure 3. This virtual reality environment for an IGCC plant offers realistic training opportunities
Another application where 3-D reality modeling has great potential is in asset management. Bentley Systems, Inc. (Exton, Pa.; www.bentley.com), for example, offers software that can combine photos taken from the ground, from drones and from laser scans to create 3-D reconstructions of facilities. These reality models can be used for planning maintenance, construction, training and more.
Process modeling and simulation capabilities are increasing as software becomes more advanced and more readily available (see A New Mentality in Process Modeling, pp. 22–25). One of the areas gaining momentum is in moving from steady-state process optimization that is run periodically, to continuous dynamics optimization and control. So called "digital twins" are realtime dynamic models that run alongside a functioning plant. These dynamic models can use data from sensors installed in the plant to match its realtime status and condition, and to carry out off-line dynamic studies to help optimize its performance. These digital twins can also be used to train operators. Vendors such as Honeywell Process Solutions and others offer digital twin technology (also see Refineries Explore IIoT Tools to Maximize Profits, Chem. Eng.May, pp. 16–20).
Convergence of IT, OT and ET
To draw the full benefits of the digital transformation, cultural changes are needed in addition to technological ones. A better working relationship between operational technology (OT), information technology (IT) and engineering technology (ET) has been cited as an important step. Greg Gorbach, vice president of the ARC Advisory Group (Dedham, Mass.; www.arcweb.com) says, "Chemical companies are revisiting their own business processes and technology approaches as competitors and partners start to employ ‘digitalized' business processes and exploit the increasing convergence between OT and IT on the plant floor, to connect the enterprise as a whole to the extended supply chain and throughout the ecosystem."
One of the areas where this convergence is most needed is in cybersecurity. While cybersecurity on enterprise IT has been well defined with firewalls, routers, anti-virus software and more, the needs on the OT side are less well defined. Eddie Habibi, CEO and founder of PAS Inc. (Houston, www.pas.com) says "Operational technology used to be thought of as ‘cyber-immune,' but we've come to know that OT is also vulnerable." Because "we cannot know what the cyber hackers are thinking or will be doing next," Habibi sees cybersecurity as a compelling need for IIoT. On the OT side, he says that there are a tremendous number of assets that are unprotected, and part of the problem is that owners are often not aware of what cyber assets they have. Taking an inventory is a first step that he recommends. And on the cultural side, training employees in cybersecurity – even the most basic steps – is much needed.
The new technologies and advanced computing that are now available with the dawn of the digital transformation offer amazing possibilities. To put it into perspective, Dow's Bardin offers the following insight: "A key in this environment is to determine what makes sense for your business, develop a concise strategy that will achieve the desired objectives, and stick to the principles of that strategy to screen out the hype in order to find the nuggets of technology that can provide true, long-term benefit." ■
Dorothy Lozowski