Drones are quickly entering the chemical processing space as more companies begin to embrace their use for inspection and monitoring tasks
There is no doubt that drones, or unmanned aerial vehicles (UAVs), hold many promising opportunities for the chemical process industries (CPI), although, as with any new technology, some challenges may arise. "We're just starting to see some of the larger chemical manufacturers begin to use drone technology," says Bill Erny, senior director of security, regulatory and technical affairs at the American Chemistry Council (ACC; Washington, D.C.; www.americanchemistry.com). Equipment inspection, says Erny, is currently the most promising application for drones in the CPI. "Some equipment is challenging to access, such as flare stacks, large processing vessels and things of that nature," he explains. Some drones can actually fly inside equipment structures and execute visual inspections, or even non-destructive testing (NDT), eliminating the need for confined-space entry. Although equipment inspection is currently the most commonly seen application for drones in CPI plants, several other tasks have emerged where their use might be beneficial, including emergency response, security management, site surveys and environmental remediation.
While drones certainly hold potential to provide security services, there are also some concerns associated with the unauthorized use of drones near chemical processing facilities. Commercial drone usage in the U.S. is regulated by the Federal Aviation Administration (FAA), but it has fallen to individual states to provide guidance on recreational or otherwise unauthorized drone usage near critical infrastructure, including chemical plants. Domestically, drone complaints have mainly been nuisance-related, but the potential is certainly there for more insidious actions to take place. "One of the key considerations here is to establish a mechanism where operators can report concerns about unauthorized drone use, and establish a formal mechanism for notifying the general public where recreational use of drones is not permitted," explains Erny. He emphasizes that the ACC supports future legislation regulating the use of unauthorized drones and for the FAA to fulfill its mandate to create new rules prohibiting the unauthorized use of drones near critical infrastructure.
Aviation and the CPI collide
The proliferation of drones into more and more applications has necessitated collaboration between the aviation and industrial sectors. Drone service provider AETOS Group (LaPorte, Tex.; www.aetosgroup.com) was formed by a group of commercial pilots in 2010, and began collaborating with a major global CPI company in 2011 to evaluate drone applications in chemical plants, focusing on safety and regulatory issues. In late 2015, AETOS was bought by Mistras Group Inc. (Princeton Junction, N.J.; www.mistrasgroup.com). "Once we progressed the data that the drones could deliver, we recognized the need to take it a step further and actually start building finished products," explains Nick Harwood, operations manager at AETOS. AETOS works with operating companies to develop bespoke drones and robotics (Figure 1). "We've done several custom-builds now that are unique to specific applications," adds Harwood. "We are allowing clients to get to places they could never get to before without major expenses," he continues.
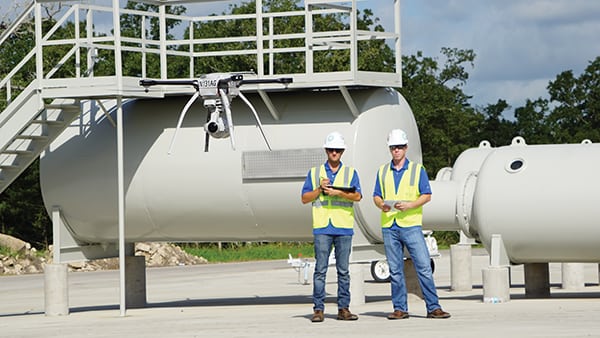
FIGURE 1. Some companies may custom-engineer a drone to carry out specific tasks, such as specialized non-destructive testing or gas detection
AETOS Group
The inspection of flare stacks is among AETOS' most popular drone services (Figure 2). "Shutting down flare stacks is extremely expensive, and with a drone you can do the inspection online, which is a huge benefit," says Harwood. Beyond equipment inspection, the company has developed drones equipped with infrared (IR) camera technology to detect leaks and fugitive emissions.
Improved drone capabilities have also enabled internal inspection of structures, such as tanks and vessels. Flying drones inside large storage tanks saves time and costs, as no scaffolding needs to be constructed and no personnel have to enter the tank (Figure 3). "In smaller pressure vessels, personnel don't have to make entry," says Harwood. He reiterates that while drone-based internal inspection technologies are still relatively new, they present benefits in numerous areas, including turnarounds and quality-control of new piping circuits.
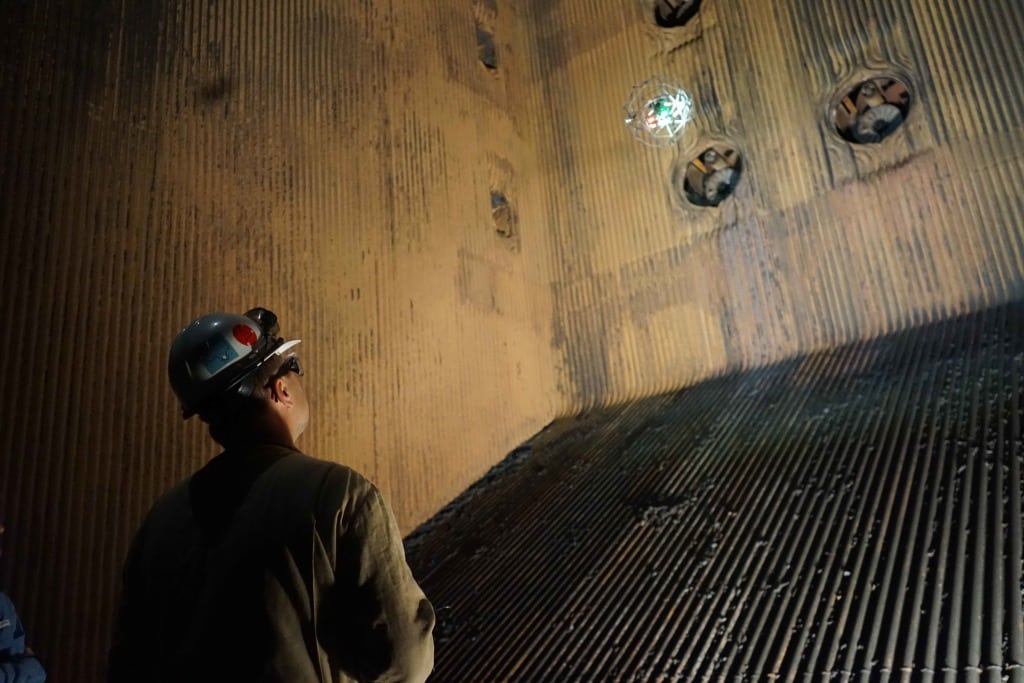
FIGURE 3. Drones flown inside of tanks, boilers and other large structures provide quick, comprehensive inspections AETOS Group
In one recent project, AETOS custom-built a "crawler" robot to go into a large vessel and complete a visual inspection, as well as two different kinds of NDT. Typically, says Harwood, these types of NDT did not occur very frequently and would require extensive amounts of scaffolding, while incurring nearly $500,000 in costs. "We were able to outfit the tools on the drone and do these inspections in a day or two, and get complete coverage, with no scaffolding," he explains. Here, the major takeaway is that with drones, certain types of specialized NDT can be done more frequently, increasing reliability.
"There's a lot of front-end work before taking a drone into a facility," says Harwood, mentioning client concerns associated with aircraft operational safety, security and equipment inherent safety. "None of the drones today are intrinsically safe, so you have to understand the processes and ask the right questions," he continues. However, he says that these limitations have not hindered AETOS' work. For instance, the cameras affixed to flare-monitoring drones have sufficient zoom capabilities – they can reportedly decipher increments as small as 1/32 in. from 60 ft away – to operate at a safe distance and still collect useful data. He says that while there are applications to justify a business case for intrinsically safe drones, the development work for these devices is still very early. Furthermore, many large chemical companies have their own internal aviation departments to rigorously vet any drone technologies being used inside plants. "We make sure to use equipment that have encrypted links that are unique to the aircraft so that they don't interfere with plant sensors, and we have also tested them thoroughly," he explains.
One company working with AETOS to develop high-performance inspection drones is Interactive Aerial, Inc. (IA; Traverse City, Mich.; www.interactiveaerial.com). The company, said to be one of the few U.S.-based drone manufacturers, focuses on drones used for internal inspections of tanks, boilers, cargo ship hulls and other large equipment (Figure 4). The drones can quickly supply a large amount of internal inspection data via high-resolution photos and video (Figure 5). What sets IA's technology apart is a proprietary laser-based navigation and collision-avoidance system, says Christian Smith, president of Interactive Aerial. Typically, "off-the-shelf" drones use global-positioning systems (GPS) and internal compasses for navigation, but these functionalities run into difficulties when the drones are inside large steel or concrete structures. "We have a laser that spins around 360 degrees on the drone for navigation, allowing the drone to learn its environment inside the tank or boiler. When it knows its environment, it offers the collision-avoidance aspect," explains Smith. While other drones do include collision-avoidance capabilities, those systems may rely on cameras that typically do not properly function in a dark, featureless environment, such as the inside of a tank. The laser-based system works regardless of the lighting conditions of its environment, says Smith, and also takes into account the tanks' walls, floor and ceiling to create a virtual "bubble" around the drone for collision avoidance. This also eliminates physical interference between the drone and the inspected surface, whereas other drones may require a "cage" around the equipment to protect against collisions, which can hinder data collection. "This allows the operators to focus on gathering inspection data, rather than not running into things," he adds.
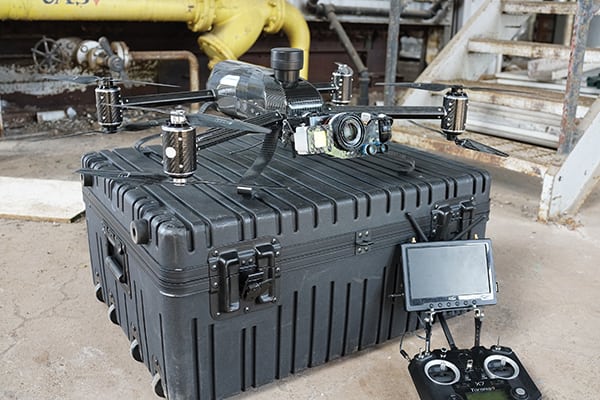
FIGURE 4. Special design and operating considerations must be taken for drones meant to be flown inside of large vessels
Interactive Aerial
Beyond inspection, IA is seeing interest in using drones for emergency response purposes, for instance in evaluating the spill of a dangerous chemical, but these applications are still very new. According to Smith, the company is working with a local Federal Emergency Management Agency (FEMA) chapter to look at potential drone applications for emergency scenarios. "If there were a chemical spill, they'd want to send in a drone first before sending in a rescue team," Smith explains. "It'll be a big part of the drone world moving forward."
Smith believes that to better harness drones' potential in chemical-handling applications, autonomous, intrinsically safe equipment is the next natural progression. Although manufacturing drones to the safety standards dictated by certain industrial classifications would be quite demanding, there is confidence that companies will begin to investigate such offerings in the near future. "If we had a fully intrinsically safe drone, we could go into tanks without requiring commercial cleaning or degassing," Smith predicts. Currently, prior to inspection, tanks must undergo rigorous preparation per American Petroleum Institute (API) 653 standards. The next hurdle would be to use drones for in-service inspections, but developing capable equipment presents considerable challenges to drone manufacturers. "We would have to re-write the way drones work, essentially, to make that happen, and we are currently researching what that would take," he says. IA has recently acquired a large decommissioned fluid-storage tank to use for in-situ test flights of its drones for demonstration and research purposes.
With regard to autonomy, line-of-sight regulations present particular hurdles for pilotless drones. Earlier this year, Airobotics (Tel Aviv, Israel; www.airobotics.co.il) became the world's first company to receive federal authorization (from the Civil Aviation Authority of Israel) for Beyond Visual Line of Sight (BVLOS) operation of an autonomous drone. In an industry first, the company has deployed its autonomous drones for data-capture at the Worsley Alumina operations of Australian mining company South32 (Perth; www.south32.net).
In a cross-industry collaborative effort, AkzoNobel N.V. (Amsterdam, the Netherlands; www.akzonobel.com) is currently working to implement its InterPlan inspection system for coatings maintenance into drone surveys, which will decrease the time and cost required for such inspections, especially in difficult-to-reach areas, such as in marine installations (Figure 6). "With the even greater restrictions and issues around access involved in working offshore, we'll see greater efficiencies and benefits during the inspection process," says Chris Langley, InterPlan product manager. In tandem with research and development group Drone Ops, coatings specialist Safinah Ltd. and tanker operator Barrier Group, AkzoNobel is working to develop drones designed specifically for coatings and corrosion inspection in enclosed areas, including ballast water tanks and offshore wind farms. The project is progressing well, and a prototype bespoke drone is currently undergoing trial flights, according to Michael Hindmarsh, business development manager for AkzoNobel Marine Coatings. The team plans to deliver a working prototype later this year, although there are many challenges to address. "The project has to overcome many obstacles associated with the inspection of surfaces in confined spaces, including navigation through very small access holes and piloting outside of the line of sight, to name just two," says Hindmarsh. In Australia, AkzoNobel is currently testing drones for inspection tasks at remote production sites where access is limited.
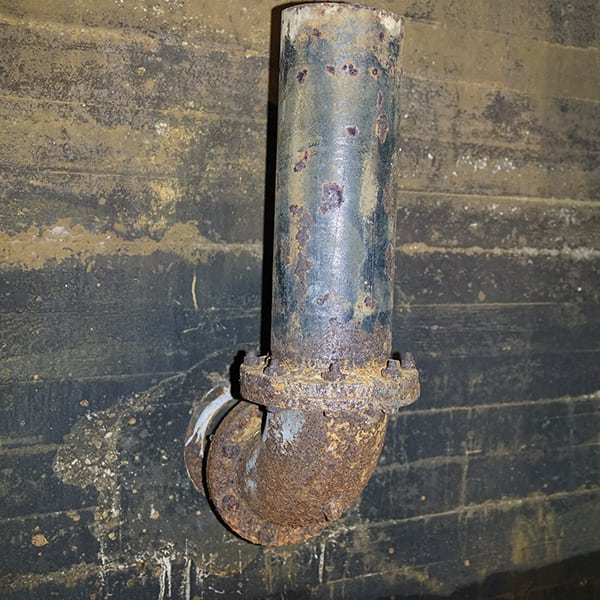
FIGURE 5. Drones can quickly provide high-resolution images for internal inspection of tanks, vessels, boilers
and more
Interactive Aerial
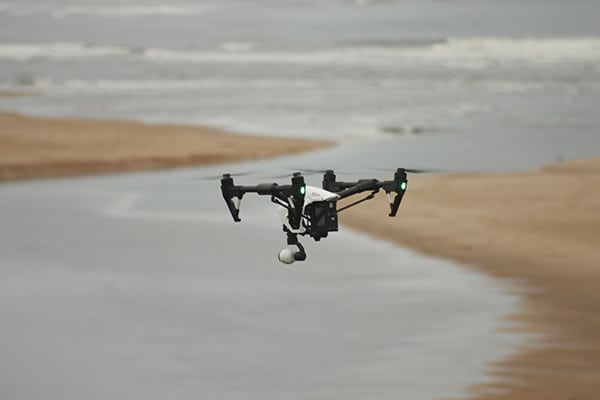
FIGURE 6. Pilot tests are currently underway to commercialze drones for the inspection of coatings in marine environments
AkzoNobel
Making the most of drones' data
Contextualizing, interpreting and organizing the massive amounts of data collected by drones is essential. At the forefront of integrating drone inspections with advanced analysis is Sky Futures (Hayes, U.K.; www.sky-futures.com). The company has recently signed expansive contracts with global manufacturing companies Eni S.p.A. (Rome, Italy; www.eni.com) and Petronas (Kuala Lumpur, Malaysia; www.petronas.com). Sky Futures not only provides drone-flying services, but also trains and encourages clients to learn how to use their own drones for everyday tasks. "The real benefits come when there is a drone on site at all times," says Colin Hickey, head of product at Sky Futures. "We've all got a laptop. Why shouldn't everybody have a drone?"
He emphasizes drones' potential to drastically shift asset-reliability practices by allowing more frequent plant assessments rather than depending on typical inspection cycles (Figure 7). "That's really the crux of what drones change. If you have a drone, you can do ten-minute flights to collect data rapidly and safely. It completely revolutionizes the way we gather information at a plant," he continues.
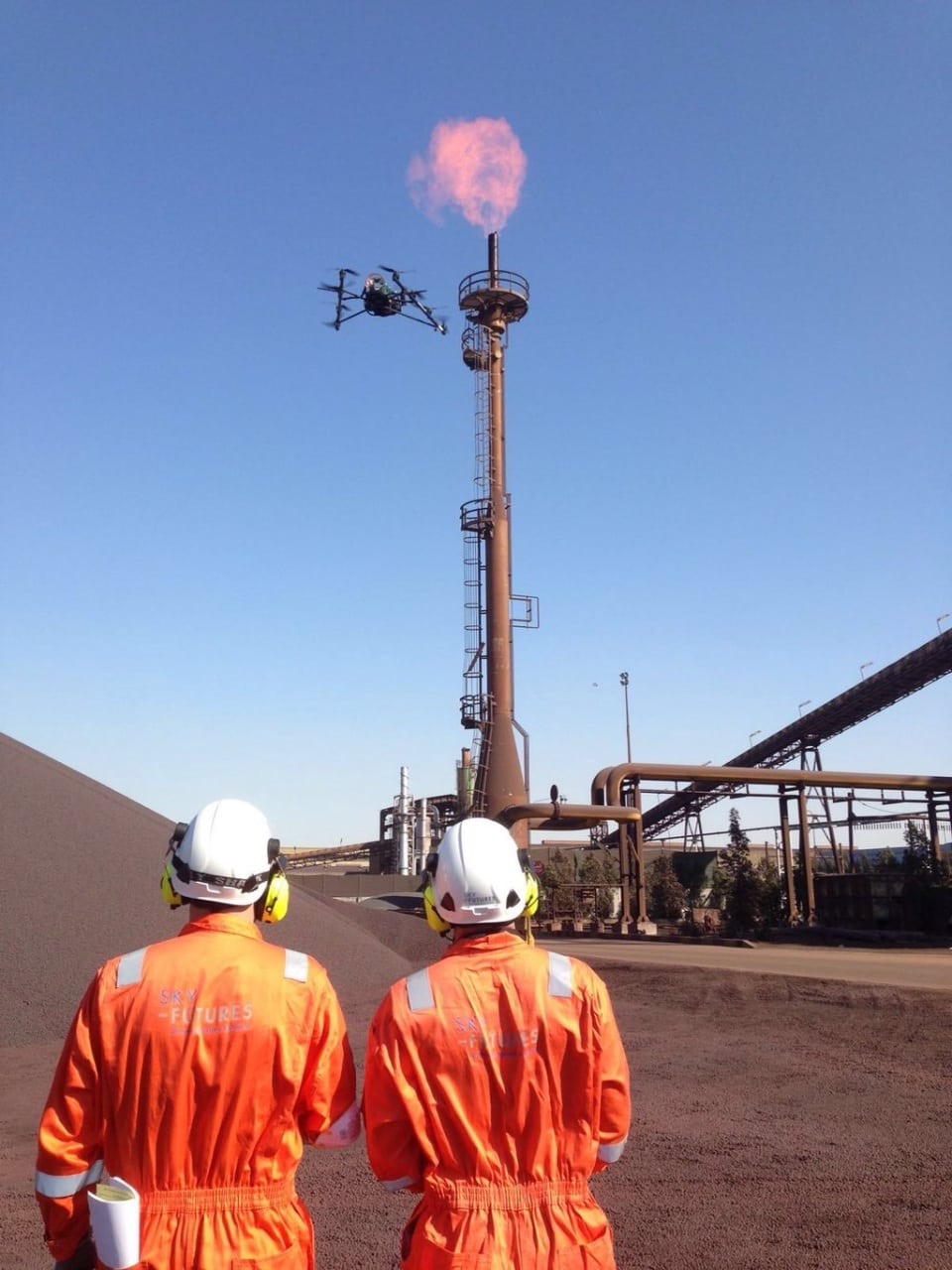
FIGURE 7. Drones may eventually become as ubiquitous as laptops for engineers working in plants Sky Futures
For instance, engineers can monitor flares with a thermal-camera drone and compare the data with the control-system feed and evaluate how the flare temperature is changing with the process flow (Figure 8). The imagery collected by Sky Futures' drones can be combined with other imagery sources, such as cameras on operator helmets or scope cameras that look inside pipes, for example, to formulate a more complete representation of the plant. "By putting all your data into a central repository, you're basically building a virtual version of the plant on your desktop that anyone can access," explains Hickey.In the past year, Sky Futures released additional imagery-analysis tools with algorithms that quickly pinpoint the most pertinent data from drone surveys, such as hot spots on pipe racks that can indicate potential leaks or corrosion under insulation. "We can process thousands of images in a few minutes and then tell operators where the faults are," he adds. Also, the algorithms can detect small anomalies that the human eye may miss, such as cracks in welds or small patches of corrosion. However, he reiterates that operators' expertise and input are still required to ensure the programs' reliability.
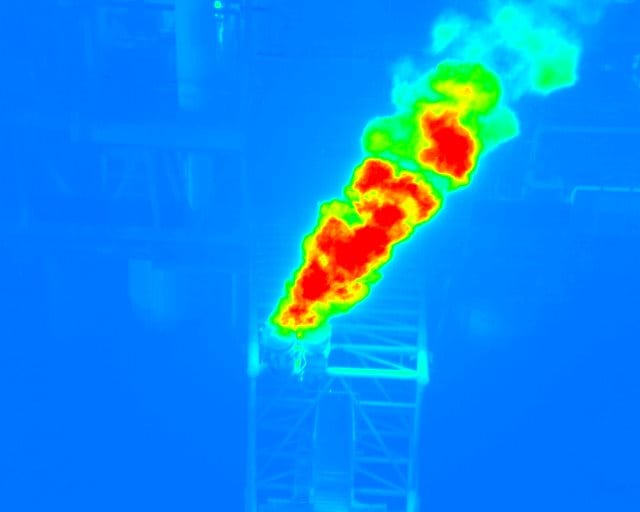
FIGURE 8. Drone-captured thermal imagery aids in rapid evaluation of flare characteristics Sky Futures
Hickey presumes that the next steps in the technology trajectory for drone-enabled analyses will involve more agile, autonomous drones that take into account weather and other site conditions to develop an optimal inspection schedule. Data would be automatically mapped and positioned onto servers and put through algorithms to allow for trending and predictive analysis. "As soon as you can spot a problem in an image, you can begin to trend that over time. That's the next thing we are working on," he says.
Designing a reliable drone can be somewhat analogous to process design. "Successful drone operators are the ones who think like process engineers," says Hickey on the importance of layers of protection in equipment design, even for drones (Figure 9). Multiple redundancies in GPS systems and duplicate propellers instill confidence in drones' reliability. However, while some organizations, including Oil & Gas UK (London; www.oilandgasus.co.uk), have drafted guidelines specific to the oil-and-gas sector, no comprehensive industry standards governing drones in chemical processing facilities are currently available. Similarly, testing and certification group SGS S.A. (Geneva, Switzerland; www.sgs.com) has written general audit standards for drone pilots, and the American Bureau of Shipping (ABS) has created certifications for drones in the maritime sector.
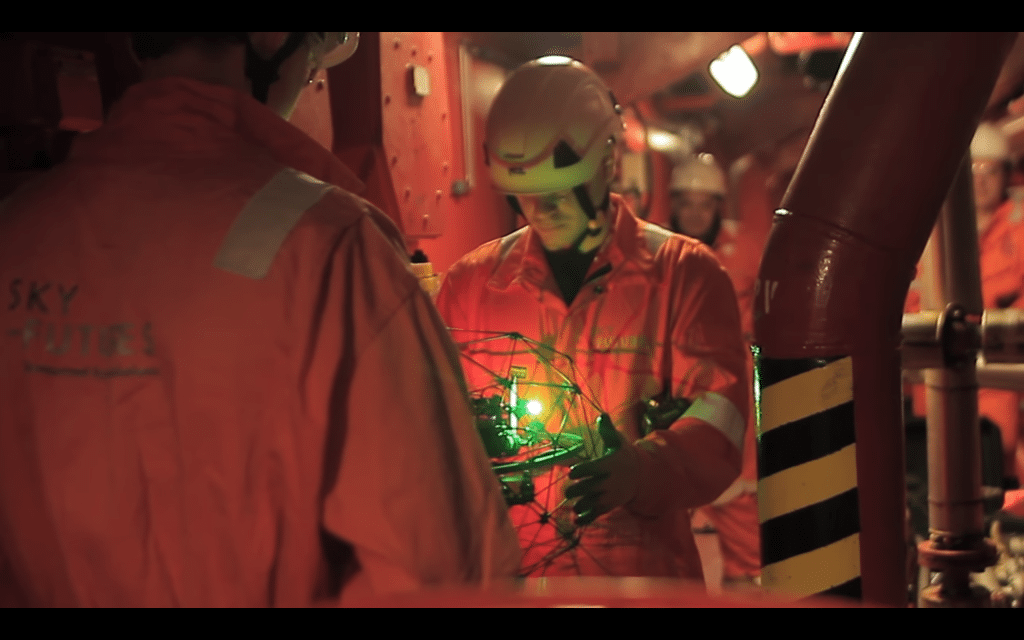
FIGURE 9. Engineers should consider safety and reliability redundancies when operating drones in chemical processing plants Sky Futures
Drone imagery becomes reality
Bentley Systems, Inc. (Exton, Pa.; www.bentley.com) is using the data-capturing capabilities of drones to survey plants with the goal of creating "digital twins" that enable robust modeling and analytics. Bentley software processes a set of drone-captured 2-D photographs and compiles them into a 3-D reality mesh for a holistic view of an entire plant's assets (Figure 10). "The technology converts digital photographs into 3-D models very quickly," says Anne-Marie Walters, Bentley's industry marketing director for oil and gas. As the circumstances for utilizing drone technology have expanded and their capabilities have advanced, users' confidence in drone safety and reliability has grown as well, according to Walters. Bentley has partnered with surveying specialist Topcon Positioning Group (Livermore, Calif.; www.topconpositioning.com) to facilitate automated cloud services that interface with drone-captured imagery. "The work with Topcon focuses on capturing the as-is condition of assets, in as close to realtime as possible, so users can quickly make decisions," explains Walters.
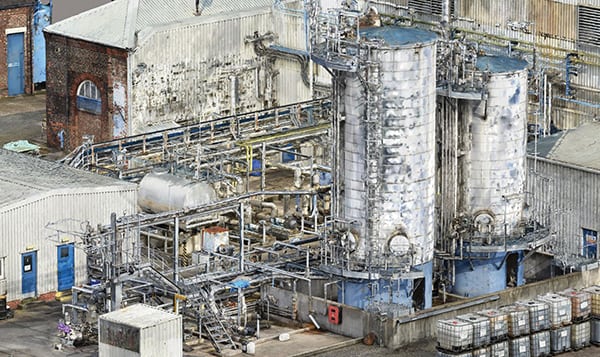
FIGURE 10. The comprehensive aerial imagery provided by a drone survey can be used to formulate a 3-D reality model of a plant
Bentley Systems
Interest in these types of aerial surveys for chemical plants began to surface in the past 2–3 years, according to Jerard Marsh, application engineer for Bentley Reality Modeling Product Development. "What the drone gives you is a full 360-degree overview of your plant that you won't get with laser scanning. You can see the tops of pipe racks, you can see around pressure vessels, so it offers much more context," says Marsh. Even a very high-level overview of a plant based on drone-generated imagery can be useful in safety reviews and brownfield site modifications. According to Marsh, several thousand photos can be captured via drones in a matter of 2–3 hours.
A wide range of CPI companies, with different end-goals in mind, have utilized drone capture and reality modeling. Walter cites several examples, including biopharmaceuticals company UCB S.A. (Brussels, Belgium, www.ucb.com), which used drones to quickly appraise the options for decreasing the carbon footprint of a manufacturing site that was built in 1928. "They basically captured a reality model of the entire manufacturing site using a drone to quickly identify and communicate the practical ideas they had for making modifications to achieve their carbon-reduction goals," Walters explains. Using drones, UCB even identified some space at the site where solar panels could be installed.
In another example, a Kansas-based ethanol producer in the midst of a facility expansion faced difficulty in gaining regulatory approval to move forward with the project due to inadequate drainage plans. A surveying company used a drone and Bentley software to develop the drainage plans in less than a week. "A traditional survey would have taken three times as long," Walters suggests.
In another case, drones were used in a situation where two adjacent steel-manufacturing plants were merged into a single facility and no overarching site survey had ever taken place. "They needed to modernize their fume-extraction system for the entire complex, but no one had ever done one overall survey of the complex," says Walters. Imagery from both photographs and laser scans were combined to generate a reality model and quickly design the extraction system. The reality model was also used to reevaluate the structural integrity of some older parts of the factory. Additional drone users seen by Bentley include a Korean thermal-power operator, and a risk-based inspection provider in South Africa.
Despite the ease of conducting surveys, processing companies still harbor some concerns about introducing drones into their facilities. However, the rapid proliferation of drones for industrial use has led to enhanced onboard safety systems. "These drones are getting so advanced now, with so many safety sensors put in place, that if anything goes wrong, the drone lands itself automatically," states Marsh. Although, as mentioned previously, no industry standards are currently available governing the use of drones in chemical plants, many companies have developed their own conservative safety and operational guidelines, in collaboration with inspection and surveying groups. "Individual companies are beginning to work out what the regulations should be locally. They go through their own rigorous safety protocol before they start to operate drones on site," explains Walters. "At the end of the day, it's just another piece of equipment you're using with your assets."
Smarter decommissioning
The many complexities of plant decommissioning and demolition require extensive planning and inspection. Dilapidated structures at long-abandoned facilities can present significant challenges and potentially put personnel at great risk. For the past few years, decommissioning specialist RVA Group (Borehamwood, U.K.; www.rvagroup.org) has been utilizing drones as part of their decommissioning services. Most recently, the company was appointed by SABIC (Riyadh, Saudi Arabia; www.sabic.com) to provide extensive decommissioning for several U.K. assets, and drones were deployed in order to inspect structures as part of the initial decommissioning strategy. "In the decommissioning arena, we are dealing with very old assets that sometimes have not been maintained for a number of years. So before we can send anybody in, we need to be sure of the safety and security of the asset itself," explains Matthew Waller, EHS & Engineering manager with RVA Group.
The remote viewing capabilities of drones provide quick and relatively inexpensive inspection of large, complicated plant structures, explains Richard Vann, managing director of RVA Group. Alongside other advanced technologies, such as ground-penetrating radar and laser scanning, drones provide inspection details that are infeasible or difficult to obtain with previous inspection techniques. "With drones, we literally get a bird's-eye view. We can fly into places where we wouldn't be able to send personnel without putting an enormous amount of manpower on the ground for initial inspections. It's given us a window of opportunity to speed up the investigatory process," says Waller. These initial inspections are especially crucial for sites where accurate records of the construction details are not immediately available, or where records may not be up to date.
Inspections are particularly challenging in long-dormant plants. "We are looking at assets on a project in the U.S. that have laid idle for 50–60 years, and they are overgrown with trees and moss. You wouldn't think of letting anyone use the access routes or the staircases," says Vann. Flying camera-equipped drones over the site revealed numerous hazardous situations, including holes in building roofs, collapsed staircases and even elements of structures that had become detached. According to Vann, the use of drones was essential in this project to understand how to best access the plant and to determine safe areas for personnel to work. "I'd rather lose a dozen drones than one person cut their finger," he says.
Of course, there are certain precautions that must be taken before flying drones into potentially hazardous areas, including plants where some portions are still operational. The first key hurdle, particularly when dealing with hydrocarbons, is safety, according to Waller. "Equipment that is to be taken into various areas of the plant must be rated appropriately for zoned areas with potentially explosive atmospheres." In some cases, the group's drones could only be used at a predefined distance from a certain asset. Also, limitations may be placed on whether the drone can fly inside of a structure, as the drones' transmission components may present a potential source of ignition. "To our knowledge, there are no ATEX-rated drones currently, but surely the market will quickly recognize this gap," says Waller.
Another concern is interference between the drone and the operating assets' instrumentation. Waller cites a project where drones were to be used nearby live operating assets, including plant-critical instrumentation. The team carried out a review of the potential for interference with drone signaling, since losing control of a drone could lead to collision with plant-critical structures with possibly catastrophic results. As a result of the review, the team implemented no-fly zones in certain plant areas to eliminate interference risks.
Another application for drones that RVA Group has found is for filming explosive demolitions. "From an engineering point of view, it's a good way to study collapse mechanisms, how a building or structure falls. From that, you can learn for future similar events," adds Vann.
Environmental remediation
Drones are also proving to be practical in the environmental and regulatory sectors. For instance, SeekOps, Inc. (Pasadena, Calif.; www.seekops.com) develops methane-gas sensors for drones. Earlier this year, SeekOps licensed a miniature gas sensor originally developed at NASA's Jet Propulsion Laboratory (www.jpl.nasa.gov). According to the company, the sensor is specifically suited for aerial configuration due to its miniaturized nature, and can detect methane in the parts-per-billion (ppb) range to precisely highlight small leaks before they begin to pose problems for operators. SeekOps is currently working toward a commercial release for drones equipped with these new sensors.
Aeromon Oy (Helsinki, Finland; www.aeromon.fi) is looking to bring drones into the emissions-monitoring arena through the creation of a sensor module designed specifically for aerial use. Weighing just 850 g, the company's BH-8 unit quantifies and maps emissions in realtime using up to eight different gas sensors simultaneously, with capabilities to measure up to 70 different gases, including combustible or explosive gases, refrigerants and VOCs, as well as particulate matter. Visualization of monitoring data is provided directly onto a map or aerial image in realtime (Figure 11). In addition to monitoring gaseous and particulate emissions, Aeromon has also enabled noise-monitoring capabilities into its devices. The company has had several successful pilot projects at industrial sites, including detecting leaks, mapping potential areas for toxic-gas release and reducing the risks associated with storing biomass by monitoring the presence of combustible gases. The BH-8 aerial sensor platform is slated for commercial release in late 2017, according to Aeromon.
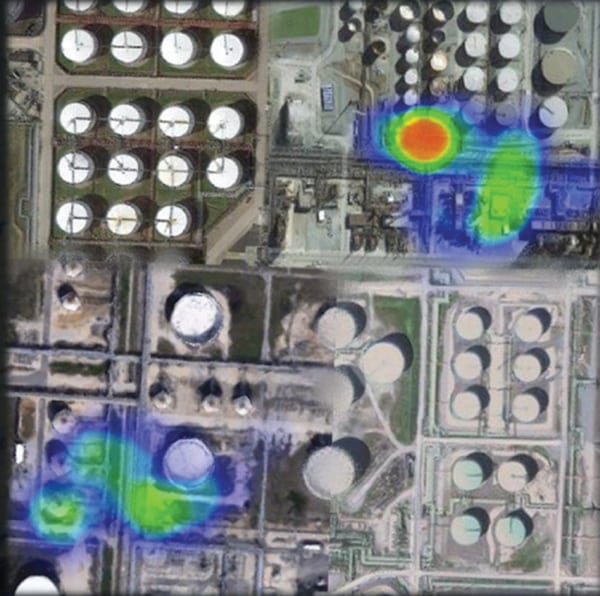
FIGURE 11. Drones outfitted with emissions-monitoring sensors can provide continuous reporting for mapping
purposes
Aeromon
The potential applications for drones extend beyond the skies into the water. Swimming – rather than flying – drones can be deployed for cleanup tasks in waterways where it might be difficult or hazardous to send personnel. RanMarine Technology B.V. (Rotterdam, the Netherlands; www.ranmarine.io) develops autonomous drones for removing solid waste or chemical contaminants from bodies of water. RanMarine's waste-cleanup drone model, known as the WasteShark (Figure 12), can collect floating debris, such as plastic waste and other solid trash. Similarly, the company's PlantShark model targets alien, or pest, vegetation, whose presence can place stresses on water supply and threaten biodiversity.
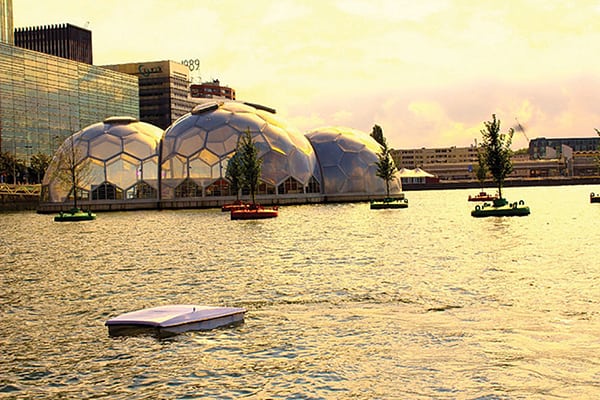
FIGURE 12. The removal of solid waste in closed waterways is aided by the use of swimming robots
RanMarine
The company's newest endeavor, the ChemShark, is equipped with proprietary internal filtration technology to remove contaminants in ports, canals, lakes or other similar bodies of water (Figure 13). According to Oliver Cunningham, RanMarine's chief commercial officer, the ChemShark is currently in the testing phase for advanced filtration technologies to efficiently remove a number of contaminants. RanMarine is working with a municipality in Sweden to deploy a ChemShark drone into a local port that has several chemical contaminants in its water, including cadmium, arsenic, copper, zinc, lead, polychlorinated biphenyl and dioxins. The company is also partnering with a potential customer in South Africa to institute a drone-based cleanup program for waste removal from a major commercial port. The company has also been investigating oil-spill-remediation capabilities for the ChemShark. According to Cunningham, RanMarine expects to have the first ChemShark in the water by early 2018.
Marine drones are a natural fit for cleaning up tight spaces in waterways where waste or contaminants may accumulate. "The value of our drones over other waste-collecting vessels is that they are smaller, more agile, lighter and cost significantly less," explains Cunningham. Furthermore, RanMarine is using solar-powered batteries in their drones, so the carbon footprint is extremely low. There is also no need for personnel to enter hazardous contaminated water, eliminating some serious safety concerns. And since the drones are fully autonomous and can run continuously, cleanup tasks can be completed more quickly. Furthermore, says Cunningham, the drones can work in intelligent teams, sharing information and effectively self-organizing to most effectively tackle the task.
One of the main concerns the company emphasized in the development of their technologies is the avoidance of unintended consequences for the ecosystem in a body of water (Figure 14). "To extract one chemical out of the water, you may have to introduce another chemical. The introduction of this new chemical might be problematic, so we are absolutely determined to think through these side effects first," says Cunningham. "We're also very mindful of wildlife and biodiversity. We've had zero animal or human injury to date," he continues. Another important consideration in the development of the ChemShark was the material of construction for the drone's hull, which has to withstand continuous exposure to harsh chemicals and potentially extreme conditions. The company decided on a silicon-resin polymer material that provides strength and resilience in corrosive marine environments.
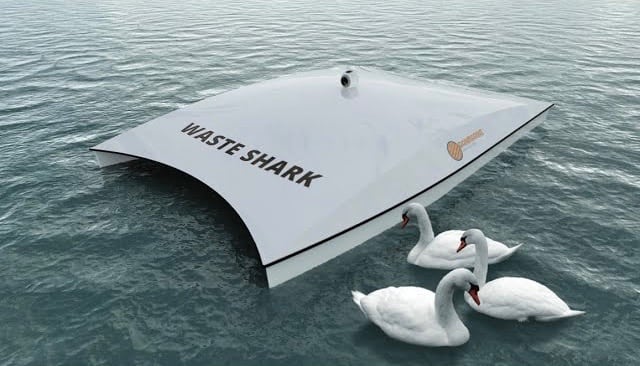
FIGURE 14. Marine robots must be designed to minimize the effects on the surrounding ecosystem RanMarine
On the horizon
The CPI's fast adoption of drone technologies for inspection purposes will likely soon expand to several other applications. The creation of consistent regulatory guidelines, along with drone manufacturers' efforts to tailor product offerings for industrial tasks, may enable drones to someday become as ubiquitous as engineers' laptops. Furthermore, research and development projects will help to craft drones for expanded applications, as more autonomous and even intrinsically safe options begin to take flight.