The shift from reactive to prescriptive maintenance can be greatly aided by advanced digital tools and the implementation of an effective pilot program
To be successful in today's industrial business environment, companies in the chemical process industries (CPI) must maximize profitability across both asset and operations lifecycles. That means continual focus on everything from how an asset is designed and engineered to how it is operated, maintained and kept running with optimal availability and uptime. At the same time, the enterprise must also optimize every second of its operations lifecycle to stay competitive.
The industrial internet of things (IIoT) continues to enable smart equipment and increase access to data. While data collected by sensors have become priceless assets to the enterprise, the ability to make sense and use them to drive new insight is where the real value lies. To improve asset performance and reliability, CPI companies are leveraging the combination of data and many different types of predictive and prescriptive maintenance strategies.
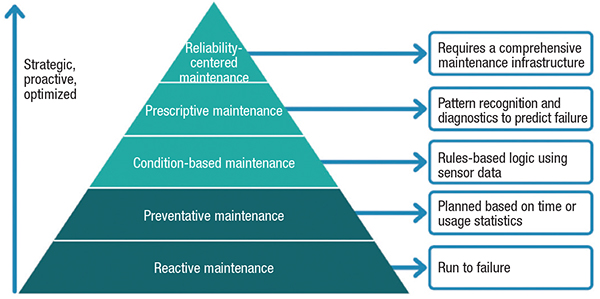
FIGURE 1. To optimize maintenance costs, engineers must consider which assets truly require the investment for advanced programs, and which non-critical assets can simply "run to failure"
Smarter maintenance through analytics
Strategic maintenance programs provide numerous benefits to the enterprise: assets can be kept running reliably with fewer failures, less downtime and related costs, and they are safer to operate – reliable uptime means that productivity is more predictable and profitable.
Outside of that, a comprehensive maintenance program makes valuable information accessible and provides context for smarter decisions. It requires a broad portfolio to collect data on assets, analyze it, determine the next course of action and use that action to further refine and optimize processes. This continuous improvement program is outlined in the maintenance maturity pyramid (Figure 1).
The higher you move up the maintenance maturity pyramid, the more proactive the strategy becomes and the more advanced warning of equipment problems is required. This enables maintenance teams to better plan resources, order materials and minimize unplanned events.
A complete maintenance program includes several approaches that are appropriate for the many different types of equipment used in CPI plants, with the goal of obtaining the greatest return on each asset.
- With reactive maintenance, the asset runs until failure. This approach is designed for non-critical assets that have little to no immediate impact on safety and have minimal repair or replacement costs. These types of equipment do not usually warrant an investment in
advanced technology. - In contrast, preventative maintenance (PM) strategies are intended to prevent asset failure. PM strategies suggest maintenance work to be conducted on a fixed schedule or based on operational statistics and manufacturer or industry recommendations. Preventive maintenance can be managed in an enterprise asset management (EAM) or computerized maintenance management system (CMMS).
- Condition-based maintenance (CBM) focuses on the physical condition of equipment and how it is operating. CBM is ideal when measurable parameters are good indicators of impending problems. The condition is typically defined using rule-based logic, where the rule does not change depending on loading, ambient or
operational conditions. - Predictive maintenance (PdM) relies on the continuous monitoring of asset performance through sensor data and prediction engines to provide advanced warning of equipment problems and failures. It typically uses advanced pattern recognition, machine learning or artificial intelligence (AI) and requires a predictive analytics solution for realtime insights into equipment health. For more information on AI, read "Artificial Intelligence: A New Reality for ChemicalEngineers," Chem. Eng., Feb. 2019, p. 14–17.
- Risk-based maintenance is a comprehensive prognostic strategy that balances the risk of asset failure with the cost to maintain assets, allowing plant operations and maintenance personnel to make decisions that support overall business objectives. As a result, the planning for maintenance and the operation of equipment exceeds safety and reliability goals while also maximizing return on asset investment.
For more complex and critical assets, a prescriptive strategy is generally the best approach. Prescriptive analytics enables personnel to detect and address subtle variations in equipment behavior before they become problems that significantly impact operations. Unscheduled downtime can be reduced because personnel receive early warning notifications of developing issues. Maintenance costs can be reduced due to better planning, and parts can be ordered and shipped in advance to avoid delays, which means equipment can continue running. Additionally, some suggested maintenance windows can be lengthened as determined by equipment condition.
Prescriptive analytics in support of a PdM strategy are also helpful in identifying issues that may not have been found otherwise. According to a study of common failure patterns by ARC Advisory Group (Dedham, Mass.; www.arcweb.com), only 18% of asset failures had a pattern that increased with use or age [1]. This means that traditional maintenance alone is not enough to avoid the other 82% of random asset failures – a more advanced approach is clearly required. Prescriptive analytics software can use historical operational signatures for each asset and compare it to realtime operating data to detect subtle changes in equipment behavior. These software tools can identify changes in system behavior well before traditional operational alarms, creating more time for analysis and corrective action.
With prescriptive maintenance, personnel know where inefficiencies are and can detect and react accordingly. A prescriptive maintenance strategy allows workers to understand why issues occur and use this information to understand the impact of performance deficiencies on current and future operations. This information also helps users assess the risk and potential consequences associated with each monitored asset, and can also be used to better prioritize profitability and operational expenditures. As a result, the planning for maintenance and the operation of equipment is safer and more reliable.
Analytics for lifecycle management
Prescriptive analytics are also very useful for "what-if" scenarios. By combining realtime and historical data, operators can assess potential outcomes of operational states and behaviors based on multiple variables. Deterministic or non-deterministic models can then be applied for open-loop simulation and prescriptive analytics. For example: Given the turbine's current maintenance state, how long can it run before failure and how likely is it to fail?
To make this analysis possible, data must be captured and turned into actionable insight through four key processes:
- Connect people, processes and assets using digital technology and tools that increase operational safety, efficiency
and agility - Collect and contextualize the data your enterprise generates to increase situational awareness across key performance and scorecard indicators
- Analyze information with machine learning and advanced pattern recognition to drive predictive insights on process and operations that identify value leaks in the enterprise and expose new
market opportunities - Act to reduce downtime, optimize asset management and maintenance, increase overall equipment effectiveness and drive new user experiences
The four steps above enable the creation of digital twins of enterprise operations and asset lifecycles. Using digital twins enables advanced modeling of everything from individual asset performance to full-scale plant and facility production optimization.
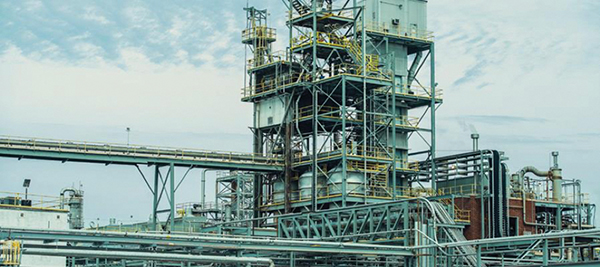
FIGURE 2. A comprehensive digital twin of an entire plant can be the ultimate maintenance strategy, in that it integrates process models and simulation with continually updated sensor data to give a full picture of operational status
Digital twins as a maintenance strategy
A digital twin is a digital representation of a physical asset, like a pump, motor, turbine or even an entire industrial plant (Figure 2). The digital twin allows operators to predict asset behaviors based on simulation of the asset in various conditions. To effectively enable asset lifecycle management, the twin requires complete and continuous data input from asset design through operations.
The process starts with unified engineering in which process design, modeling and simulation are combined with overall plant design to create an integrated engineering environment and collaboration workflow. This results in significant reduction of engineering effort, easier collaboration among stakeholders and a lower total cost of engineering.
In the design phase, the use of digital models allows analysis of processes, equipment and operations through multiple simulations for optimum safety, reliability and profitability. As the physical asset's operational life continues, a digital clone of the asset can be updated in real time.
Creating digital twins of assets allows users to optimize asset performance, reliability and maintenance. Throughout asset deployment and commissioning, the digital twin is continually updated with ongoing operational and process data, such as maintenance and performance records. The digital model uses predictive learning technology to proactively identify potential asset failures before they occur.
With the availability of low-cost sensing technology, sensor networks become another data point in generating an asset's digital twin, particularly for legacy assets that were not born digital. As digital tools, such as predictive analytics and machine learning software, monitor the physical asset and its environment through sensor networks and other data sources, a variety of cloud-based or on-premise tools can be applied to predict equipment failures before they occur while maintenance is scheduled around optimum economic and production conditions.
Most assets designed and deployed today have digital communication and connectivity built in. For assets and facilities commissioned before widespread digital connectivity, digital workforce enablement combined with mobile operator rounds and sensor technology provide a path toward creating digital twins of legacy assets while offering substantial improvement in workflow efficiency and accelerated operator training through augmented and virtual reality (AR/VR) technologies.
Empowering the workforce
Beyond maintaining physical asset reliability, maintenance strategies and solutions have broad impact across an entire enterprise. As industrial organizations manage transitioning workforces, predictive analytics solutions can help ensure maintenance decisions and processes are captured and repeatable by incoming personnel.
Other digital technologies augmented by data analytics facilitate improved knowledge transfer and increased situational awareness throughout the enterprise. For example, operator training simulators (OTS) powered by AR/VR technology bring to life digital twins of assets, control rooms and entire plants in a safe and controlled learning environment. Immersive technologies, such as head-mounted VR (Figure 3) displays and 3-D projection, allow real-world training simulation in the digital control room or plant.
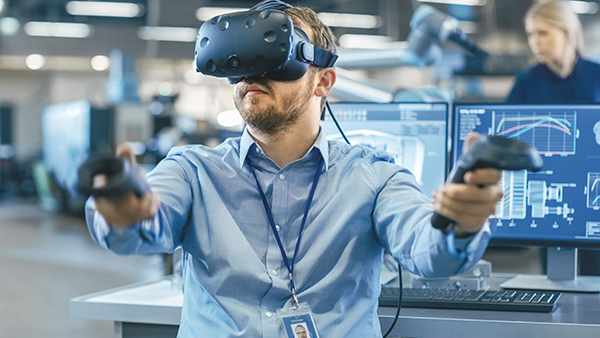
FIGURE 3. Virtual-reality (VR) training simulators can streamline the knowledge transfer between new and experienced operators
Similarly, mobile technology enables workers to collect data from non-instrumented and stranded assets, enhancing operational visibility and increasing situational awareness across all maintenance and reliability functions. Mobile operator rounds digitalize operational processes, ensuring best practices are followed by operators at all times while enabling realtime team collaboration during problem resolution. From the mobile operator, tasked with keeping systems running now, to the reliability engineer focused on ensuring systems will run tomorrow, mobile technology is a driving force behind digital transformation.
When these technologies are coupled with digital twin technology, operators and plant personnel can begin to visualize processes and assets in real time, accelerating new insights on enterprise operations and improving knowledge transfer between new and experienced operators.
Getting started
Many CPI companies are beginning their digital transformation journeys by piloting predictive maintenance solutions, which can provide an immediate and measurable return.
As part of a digital transformation journey, pilot projects of digital solutions, such as predictive analytics and maintenance, can help the enterprise understand the best technology investments to improve profitability and maximize return on capital.
To ensure an organization is able to thoroughly evaluate new technology and gain value from the pilot project, consider the following guidelines.
Recruit leadership support. With any technology project, it is important to get buy-in from the executive leadership team. Some leading companies have even developed specific teams focused on digital transformation to ensure broad support.
Define scope and success at the start. To ensure success, you first need to define what that looks like. A good partner will work with you to identify specific and measurable outcomes that will result from implementing the technology. The focus of the pilot should not be to define a business case, but to instead prove a business case. For example, proving that the software can predict equipment failures to avoid significant repair costs.
Create a timeline.It is critical that a timeline is attached to the pilot program that specifically defines a deadline to officially adopt the technology. If the technology's value cannot be proven within that timeline, it may be best to move on to alternate solutions.
Conduct formal project management. Pilot programs require the same level of attention and discipline as a production-level implementation. Assign resources, and put a documented project plan in place before the pilot begins.
Put people first. No matter how great a new technology works, if people cannot use it, it is not worth the investment. That means putting a training program in place, and if the pilot is successful, continuing to invest in training on a regular basis.
For those organizations not equipped to handle the monitoring process internally, predictive maintenance can even be outsourced and performed in-house or offsite. Monitoring and diagnostics providers can put forward a team to manage the entire maintenance process, or to supplement internal activities through model training, diagnostics and best practices.
Regardless how an organization staffs this type of project, these services empower companies to leverage predictive maintenance, while reducing total cost of ownership.
Comprehensive digital strategies
Many benefits are realized when considering the maintenance costs that "could have been," including replacement equipment, lost productivity, additional personnel hours and so on, when a major failure is avoided. A complete maintenance strategy combines enterprise data capture with asset management, prescriptive analytics and risk-based management. Work orders can be automatically generated to relieve maintenance issues. Analytics capabilities continue to evolve from predictive to prescriptive – from what will happen to what should be done.
Edited by Mary Page Bailey
Reference
1. Rio, R., Optimize Asset Performance With Industrial IoT and Analytics, ARC View, Aug. 2015.
Author
Kim Custeau is currently the asset performance management business lead for AVEVA (Toronto, Canada; Email: kim.custeau@aveva.com). She has over 30 years of experience in industrial asset management software and services. She is currently responsible for the strategic direction, commercialization and development of AVEVA's Asset Performance software portfolio globally. In this role, she helps customers improve asset reliability and performance to maximize return on capital investments and increase profitability. Prior to her current role, she was the director of asset management at Schneider Electric.