Field service workers often log long hours at remote job sites where no two days are the same. To support daily tasks, whether they be at a power plant, oil rig, or other hard to access environments, advanced technologies have become more commonplace to get the job done.
With the rapidly evolving nature of technology and on-the-job practices, it is increasingly important for organizations to implement mobile devices that can adapt to the industry demands of the future because buying new technology every few years to keep up with the pace of change is not practical. Mobile devices that have a reliable battery life, multi-functioning capabilities, and a secure connection are essential to keep operations running safely and efficiently.
The Power of Reliable Battery Life
For any field service job, one of the biggest limitations of technology is battery life (Figure 1). Field technicians often work in the field for up to 12 hours a day. When servicing and inspecting pipelines, a technician could end up walking eight to 10 miles in one day. In vegetation management, a technician could be in the mountains for days or weeks at a time clearing vegetation to build the networks and grids needed. These environments are challenging, and productivity counts as field service organizations often measure job efficiencies down to minutes and seconds.
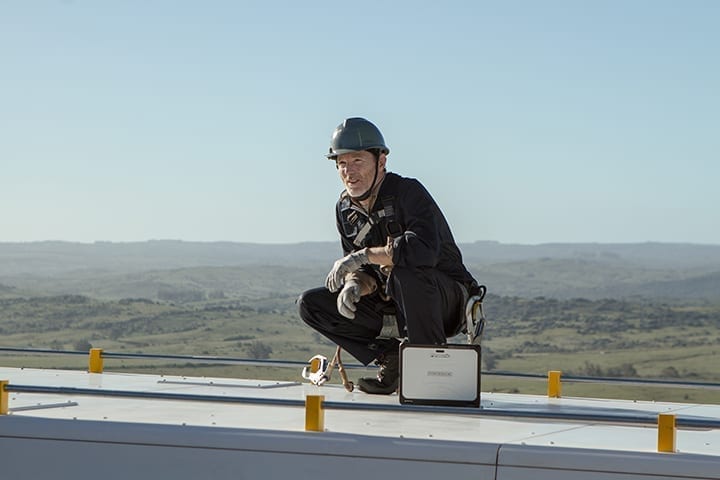
Devices with long-lasting battery life are an essential part of getting a job done. In remote areas, power sources to charge devices may be miles or days away. If a location is nearby, pausing to recharge a device can be disruptive and unnecessarily extend the workday, limiting the number of jobs completed in a single shift.
In natural disaster situations such as hurricanes and tornados where power outages are common, mobile devices with extended battery life are relied on to support essential worker communications and provide real-time access to data and information to make decisions (Figure 2). In situations where one battery does not last long enough to see the job through from start to finish, having the flexibility to input spare batteries without disrupting the device's current workflow has proven to be a game changer for workers. Equipping workers with hot swap batteries also avoids needing to shut down the device entirely with the potential of losing essential data in the process.
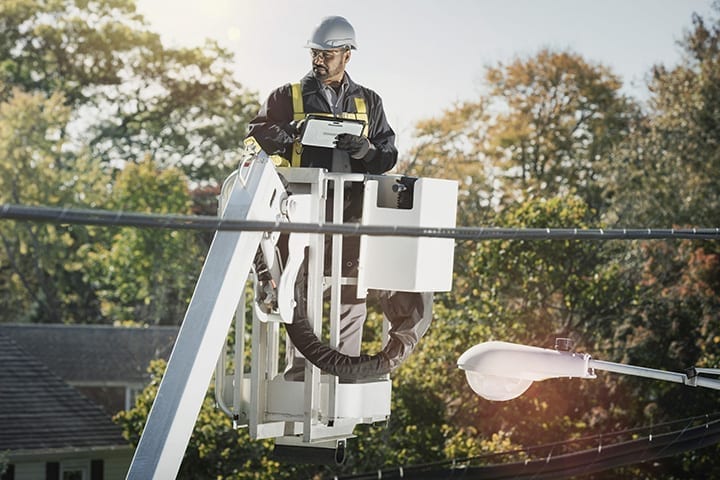
Multi-Functioning Capabilities
U.S. utility companies will spend about $500 billion over the next five years on infrastructure improvements. When planning for these investments, they will need to adjust to new mandates and regulatory uncertainty as grid modernization becomes more complex, data becomes more digital, and the infrastructure becomes more connected and wireless. Implementing multi-functioning devices will only enhance the user experience and a company's bottom line.
Specifically, energy companies and nuclear power plants require constant maintenance and inspection as the associated environments are very high risk. Workers in the field are required to test many different kinds of equipment and gages, which typically rely on multiple devices. Being able to have one device that can do multiple tasks can help consolidate the worker's toolset. The consolidation of the toolset can also make the job more efficient as the worker does not need to power up multiple devices or applications to complete a single task.
Companies specifically look for devices with multiple uses as they want their workers to have the best technology capable of getting the job done, yet they do not want workers carrying too many devices into the field at once for safety reasons. For example, built in radio frequency identification (RFID) tags on mobile devices can better pick up data and information when walking throughout a site rather than needing to take pictures or touch the equipment, which requires additional interactions and time.
A customized mobile device also has added benefits as its modular design allows operators to change modules in the device without having to buy completely new devices or send the device off for updates or upgrades. "Modularity allows us to standardize on one specific model across all business operations and add specific modules later, as needed, that don't need to be budgeted due to cost of not replacing a mobile device," said a senior engineer at a large utilities company in the southeastern U.S. A piece of the device can simply be exchanged for a new piece, avoiding disruption of needing to wait for an entire device to be serviced.
Device features like screen brightness and sunlight readability are added design benefits of solutions built for the utility and field work environment. The better the screen technology, the better off the user is, especially when it comes to touchscreen sensitivity. A day on the job typically includes a lot of logging information and scrolling through long manuals. A day on the job may also require the work to be done in humid conditions, rain or snow, or with dirty or greasy hands. A device that can quickly identify touch and distinguish a human finger wearing some type of glove from a raindrop or other weather-related distraction are essential functions in the environments these devices and workers are deployed in.
Perhaps one of the most critical features a mobile device needs to have is a dedicated serial port, not just a USB port. Companies with legacy devices look for this feature to ensure their existing yet outdated products can continue to function, and that they're able to be connected to and managed. This allows the organization to troubleshoot, diagnose, or connect to all the devices in the field to keep business running. Although not every task requires a serial port, offering this capability as an attachment allows organizations to offer it to the workers who need it. The organization can then also scale their own operations wherever needed because they have the ability to do so with their existing and newly integrated equipment.
More Cybersecurity Protections
Security used to be a part of a utility company's IT team, but over the past four to seven years, it has established itself as its own entity within the industry, especially as business functions digitalize. Cybersecurity has become so important for large organizations as well as some smaller organizations that they are investing in the talent needed to build out a cybersecurity team to solely focus on ensuring the digital safety of information and devices. Once the team is established, the organization can then assess the attack surface, where vulnerabilities exist and how to prioritize security initiatives to reduce that risk.
Due to COVID-19, the North American Electric Reliability Corp. (NERC) has asked the Federal Energy Regulatory Commission (FERC) to delay the implementation of seven reliability standards, one of which is related to cybersecurity. This new standard would require entities to develop and implement supply chain cybersecurity risk management plans and implement new controls. Although this standard could be delayed, organizations can potentially use the extended time to implement device securities of their own to be ready for these impending regulatory cybersecurity standards.
To handle cybersecurity risk on the device side, there are a few ways organizations are addressing proper authentication. One way is by deploying units with their own system's image so when the end-user, such as a line worker in the field, goes to enter their personal password, they are automatically connected to the company's server. This is achieved by having the home page of a device populate with a company-branded image and its network reflective of the security features put forth by the company, essentially being an extension of the corporate network settings.
Organizations may also initiate dual- or tri-factor authentication, which requires the worker to input a passcode to ensure the registered user is the one working within the device. Devices may also come with fingerprint identification, so for a user in the field, they can simply scan their fingerprint to verify their identity and get into the device. Some devices even use facial recognition to grant this access. To ensure devices are used for the company's purposes, other organizations have restricted or limited access to personal social media and communications platforms. Similarly, organizations do not want workers putting external unsecured devices, such as USB hard drives, into a company's own managed devices so they have implemented security measures internally and externally to ensure only company approved devices are recognized by each other.
Employees in the field also need technology to keep them concentrated on the road when driving from location to location. To achieve this, a device's security mechanisms can be equipped with motion-sensing technology that can identify when a vehicle is in motion and subsequently locking the screen to only display essential information, such as mapping or route information (Figure 3). In fact, many utility and energy companies have created their own mapping system to ensure a reliable, safe connection out on the road while keeping the driver's safety top of mind. If a driver does need to access a different part of the device, a second driver is needed to unlock and use.
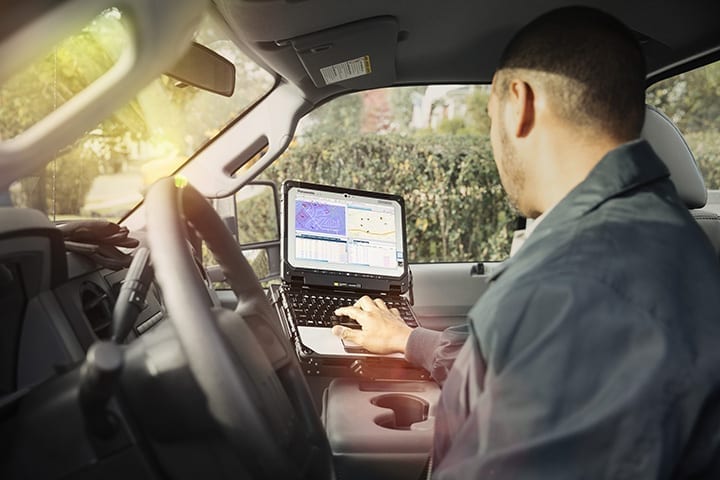
From reliable battery life to power devices, to multi-functionality, to device security, mobile technology is impacting the utilities industry across every sector. Field service organizations must make investments in high-quality tools, and computing technology is a critical part of that toolbox. Digital transformation within the industry is being led by the advancement of modern mobile solutions built for the job at hand, and future proofing deployments means investing in the right devices today to prepare mobile workers for the work of tomorrow.
–Timothy Dwyer is senior territory area manager with Panasonic Mobility.