Modern combustion technologies help processors safely meet emissions standards, while optimizing the process
Combustion is integral to many chemical processes; however, it is not without challenges. Safety is, of course, always paramount when it comes to fired equipment and constantly changing and tightening permissible emission levels are becoming more arduous to meet. If these concerns aren't enough, higher efficiencies, more flexibility and greater reliability from combustion equipment are also required. As a result, combustion often becomes a difficult balancing act.
To help meet these needs, burners that offer the lowest possible emissions are being made available and are usually combined with a burner management system that offers top-notch safety. More recently, controls, monitoring systems and instrumentation are being employed to provide greater efficiency and reliability. Together, this equipment helps optimize today's combustion processes.
A balancing act
"Safety, environmental performance and reliability are the primary challenges when it comes to designing and implementing any combustion system, and a lot of these requirements revolve around prescribed standards or internal guidelines," explains John Becker, national sales manager – business development, with Profire Energy (Lindon, Utah; www.profireenergy.com). "All these factors dovetail each other. Safety is critical and necessary and will never be sacrificed to gain efficiency. While safety is the common denominator for combustion systems, processors are often faced with balancing the efficiency, flexibility and reliability of the fired device with its environmental impact."
Further adding to the challenge is the fact that there are many combustion processes in a chemical plant, each with a different purpose and goal. "There is a large variety of combustion applications in a chemical plant, which leads to different challenges that depend upon the purpose of the process," says Paolo Schmidt-Holzmann, department manager, Proposals Combustion Systems, with Steinmüller Engineering GmbH (Gummersbach, Germany; www.steinmueller.com). "But the overriding factors that govern all combustion projects include safety, reliability and flexibility. Whether it is a change implemented on existing components or the installation of new components, operation of the plant under safe conditions must be certain."
Schmidt-Holzmann continues to say that efficiency, reliability, low emissions and flexibility are also important goals and these can change, depending on the requirements of the project. "Following safety, other priorities depend upon the task you would like to fulfill. For example, in a residue combustion project, the reliability and availability might be of higher value than fuel conversion efficiency. But in cases where very specific gas streams are produced with very specific characteristics, the fuel efficiency and reliability might be the focus."
So finding the proper balance for each combustion process becomes dependent upon designing and installing the appropriate technologies. "It's not an easy task," says Profire Energy's Becker. "Safety is at the top of the list of concerns, so there are governing bodies and internally developed guidelines that provide direction and standards to follow. Then, you must add in the aspects of the [U.S.] Environmental Protection Agency (EPA: Washington, D.C.; www.epa.gov), plant owners and third-party agencies that have requirements about what is allowed out of the stack and that has led to the design of better burners that reduce NOx and CO production."
He continues: "So when you look at the environmental aspects, you look at the burner. When you look at safety, efficiency and optimization, that's where automation and controls come in to fine tune the process based on temperatures or other factors tied to the fired devices."
Better burners
Burners are evolving every year to include new techniques and designs with different orifices, features and fuel-ratio measurement technologies to help achieve better, more environmentally friendly combustion, which is a necessity in the ever-changing environmental landscape.
"One of the biggest challenges is that the emission rates around the world for NOx and CO are getting lower and they vary by regions around the world, as well as locations within those regions," says Rex Isaacs, chief technical officer with Zeeco (Broken Arrow, Okla.; www.zeeco.com). "As a result, burner technology is getting better from all manufacturers. Often this involves looking at ways to pull in more fluegas for circulation, which lowers NOx emissions. Some manufacturers look at lean premixing to achieve lower NOx emissions. Burners are modified for more fluegas, which also helps lower emissions during start up and lower CO emissions."
Zeeco's Free Jet Power Burner is one such example. The burner uses technology that adds fuel staging to the Venturi design and free jet mixing theory, which reduces emissions in some applications to as low as single-digit numbers. The clean, fuel-conservative system operates on refinery gas, natural gas or dual fuels and offers 9 parts per million (ppm) NOx, sub-50 ppm CO with minimal external fluegas recirculation (EFGR) or 30 ppm NOx potential without EFGR, as well as a 20:1 fuel turndown potential. When coupled with the company's burner management system, it ensures the process remains in compliance while maximizing efficiency and eliminating downtime due to aging controls.
Often industry emissions regulations force users to adopt fluegas treatment solutions, such as selective catalytic reduction (SCR) systems; however, the new Solex burner from John Zink Hamworthy Combustion (Tulsa, Okla.; www.johnzinkhamworthy.com), can achieve 5 ppm NOx emissions across a range of fuel compositions and furnace temperatures (Figure 1). The burner is designed with two significant combustion zones to achieve these emissions levels from startup to full-capacity with minimal CO emissions. In addition, it produces compact flame lengths, which solve many issues ultra-low NOx burner technologies face.
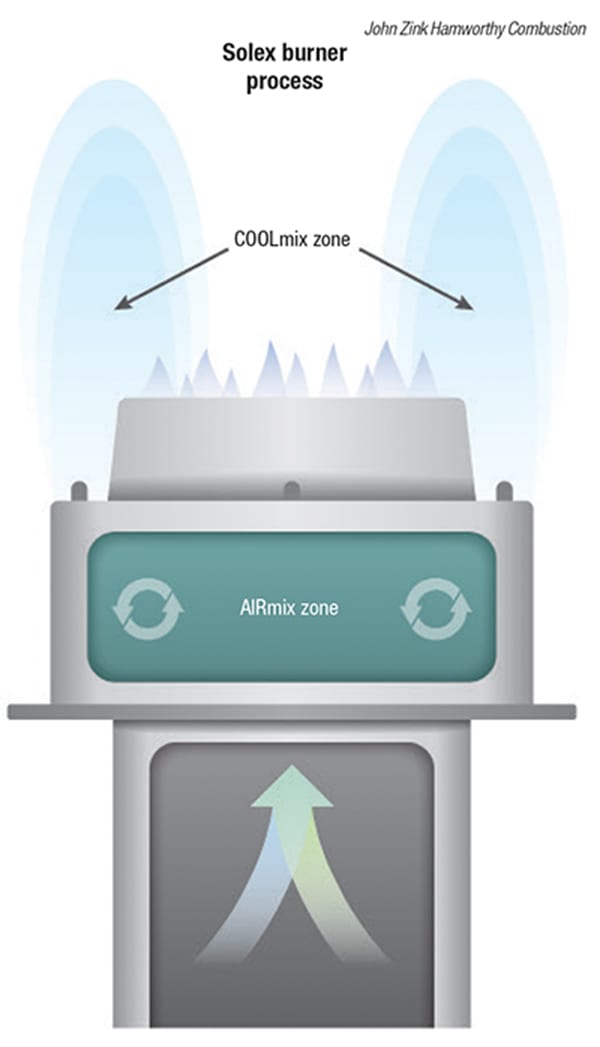
Figure 1. The Solex burner can achieve 5 ppm NOx emissions across a range of fuel compositions and furnace temperatures. The burner is designed with two significant combustion zones to achieve these emissions levels from start-up to full-capacity with minimal CO emissions
"This is the next step-change in burner technology that can be applied to reduce emissions in process heaters," says Eric Gebhard, senior sales engineer, with John Zink Hamworthy Combustion. "And, it has been strategically developed to eliminate the need to apply an SCR. The burner is designed with two combustion zones that are dynamically operated to achieve these emissions through the entire operating range."
Controls for safety & optimization
More and more, automation and controls are being employed to improve safety and optimize the combustion process. For example, burner management systems are employed on combustion processes to facilitate safety, while combustion control systems are used to meter fuel and airflows to increase efficiency.
"Burner management systems take care of safety issues, such as sequencing the lighting of the burners, going through a safe startup process, monitoring to make sure everything is within limits and automating emergency shutdown, if necessary," says Jack Valentine, general manager, with Pacific Combustion Engineering, a strategic division of Nationwide Boiler (Washougal, Wash.; www.nationwideboiler.com). "Combustion control systems control the fuel-to-air ratio of the burner, which provides better control, more efficiency and a more economical operating system. They are separate systems but they have to work in conjunction with each other."
Because burner management systems provide safety, it is important to protect them against different types of failures, says Charles Fialkowski, director of process safety with Siemens (Harleysville, Pa.; www.siemens.com), including everything from memory failure to corruption to lost I/O signals and communications to the application program being compromised. "In the past, designers used to apply generic equipment with costly external solutions to protect against these known failure modes, but today, modern, safety-certified equipment is able to handle and protect against these events. Safety-certified equipment has these safeguards built in, tested and certified for the program you're running," he says.
Siemens offers its Simatic SIS Compact as a stand-alone, safety PLC (programmable logic controller) certified solution for process safety that was designed specifically for use in safety-critical applications, such as burner management systems (Figure 2). The system leverages field-proven and certified Simatic hardware and software components, which automatically provide dedicated Safety Instrumented Systems (SIS) functionality. The SIS monitors critical processes and performs immediate and automatic responses to the process when a problem occurs without the complexity of an integrated distributed control system (DCS) solution.
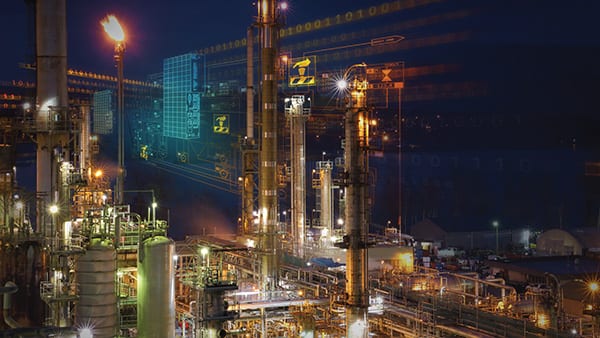
Figure 2. Siemens SIS Compact is a stand-alone, safety PLC certified solution for process safety that was designed specifically for use in safety-critical applications such as burner management systems
Source: Siemens
Profire has developed its 3100 platform to provide an alternative to traditional burner management systems with a PLC, modular-based design that allows quick configuration, intuitive alarm and a packaged burner management system, says Becker. A module is made up of an enclosure and one or more cards. Each module is certified with the appropriate regulatory bodies to ensure that installation is as quick as possible. The entire system is made up of modules and is intended to expand to accommodate future needs and applications. It can be used to control multiple burners and manage a single appliance or to control multiple pilots and manage a single appliance via one user interface. Up to 32 modules can be combined to control a variety of natural draft appliances from a single user interface. Profire's integrated I/O technology can also be used to take control of specific forced-air applications.
In addition to these safety systems, adds Zeeco's Isaacs, more chemical processors are adding additional layers of safety to their burners and burner management systems. "Ten years ago it was not common to see flame scanners on process burners in chemical plants, but now we are starting to see scanners on each burner," he says. "Flame monitoring is linked to the control room so that they can see that each individual burner is firing to ensure safety. In addition, electronic ignition can be used with flame scanners so they can light the burners from the control room and ensure that the flame is on via the flame scanners before operators go out to the furnace. This isn't the norm yet, but it is a trend processors are starting to explore more readily."
John Zink Hamworthy Combustion's Gebhard agrees: "We are seeing customers going to more automated systems and it is mostly safety driven. However, we are also seeing processors adding more control and sensors to help better optimize the overall performance of their units."
As such, the company recently launched a "Smart Combustion" initiative, which includes a variety of digital solutions that can be used to further optimize combustion systems. One such technology is the ZoloSCAN combustion monitoring and diagnostic system, which is used for combustion optimization (Figure 3). The technology employs wavelength–multiplexed, tunable-diode-laser absorption spectroscopy (WM-TDLAS), which combines lasers and fiber optics to measure and profile the combustion zone across multiple paths. The information provided by these in-situ measurements allows operators to balance, optimize and automate combustion for higher efficiency, along with lower NOx, CO and CO 2 emissions. "This results in improved efficiency and higher process yield while increasing equipment life," says Gebhard.
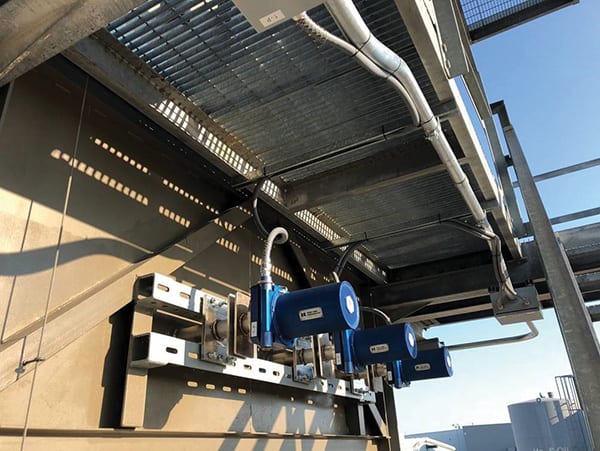
Figure 3. The ZoloSCAN employs wavelength – multiplexed tunable diode laser absorption spectroscopy, which combines lasers and fiber optics to measure and profile the combustion zone across multiple paths. The information provided by these in-situ measurements allows operators to balance, optimize and automate combustion for higher efficiency along with lower NOx, CO and CO2 emissions
Source: John Zink Hamworthy Combustion
Masanari Yokogawa, manager of the Analytical Product Sales Division in the IA Products and Service Business Headquarters at Yokogawa (Tokyo, Japan; www.yokogawa.com), adds that this type of optimization is important. "Combustion systems use large quantities of costly fuel, so operation managers responsible for large furnaces are faced with the triple challenge of minimizing costs while maximizing output and ensuring safety at all times," he says. "Currently, air-to-fuel ratio control is only used on a few systems, and fewer still compensate for changing fuel composition. Conventional technology typically only provides automated control of the fuel supply and not the air supply, so excess air is often used in the combustion process. This increases costs, reduces efficiency and creates an unsafe situation."
The ability to continually measure methane, O2 and CO levels is critical to maximizing efficiency and safety. Conventional analyzer technologies only provide spot measurement, so they can't capture the combustion condition throughout the furnace. Instead, he says, the recommended method is to use a tunable-diode-laser-spectroscopy (TDLS) analyzer in the tail of the radiant section of a combustion furnace to measure O2 (Figure 4). "TDLS analyzers deliver direct and realtime measurements using long-path average measurement across the furnace. This can be used to control the air-to-fuel ratio and to control CO to ensure safety," he says.
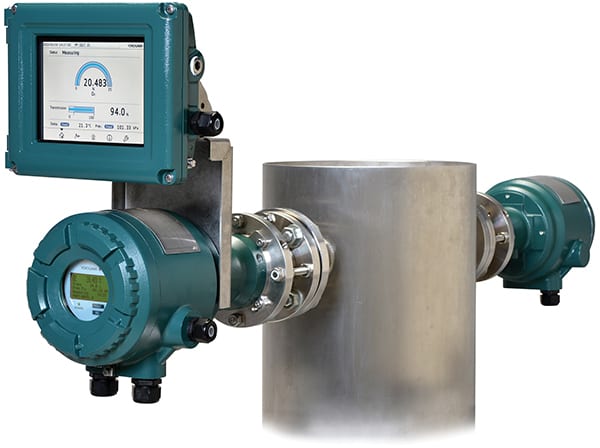
Figure 4. TDLS analyzers deliver direct and realtime measurements using long-path average measurement across the furnace. This can be used to control the air-to-fuel ratio and to control CO to ensure safety
Source: Yokogawa
While most fired heaters use natural draft rather than a forced air supply, continuous measurement enables proactive airflow control, he says. To control combustion in a fired heater, the fuel flow and arch draft can be managed through the existing plant DCS or other logic solver, while combustion airflow can be controlled directly by a CO override function. "TDLS technology provides the data required for real-time control of the combustion process," says Yokogawa. "This safely minimizes excess O2 concentration, resulting in higher heat-transfer efficiency and longer maintenance cycles for the furnace."
And, for specific combustion issues where very accurate temperature measurements across a wide dynamic range are required in order to optimize a combustion process, thermal imaging may be a useful tool, says Christopher Leonard, director development and product management with Ametek Land (Dronfield, England; www.ametek-land.com). The company's NIR-B 3XR near infrared borescope can be used to help optimize thermally driven processes. For example in the oil-and-gas industry within steam reformer applications, says Leonard, the temperature range between the furnace walls and reaction tubes containing the catalyst and reactants can be over a large temperature range. The reaction tubes in this application are typically made from an expensive nickel alloy, which, if the process is run just 10% below the design temperature, can reduce production capacity, yet running just 59°F too high can reduce the life of the reaction tubes by 50%. This makes it critical to use accurate temperature measurement to maximize productivity and maintain the integrity of the asset, which over the range of 1,112 to 3,272°F can be a major challenge.
In addition, he states, another example is in the glass industry, where the instrument gives operators and system builders further insight into the dynamics of glass melt tanks. The high-quality thermal images provided by the instrument enable the identification of burner imbalance, which can be used to optimize combustion and control NOx emissions, helping to reduce fuel bills and maintain compliance with environmental targets.
At the end of the day, all processors are looking to safely run combustion processes while also maintaining environmental compliance and improving their bottom line via efficiency, reliability and flexibility. Today's combustion solutions may be key to doing just that.