Monitoring and analyzing historical corrosion data can provide insights not available from manual inspection and measurement techniques
Some petroleum refiners looking for ways to improve profitability have lately turned to buying opportunity crudes from secondary sources. These crudes, while priced less than more premium feedstocks, often contain various contaminants, including solids and corrosive compounds. Such contaminants can damage processing equipment by corroding and eroding it from the inside out (Figure 1). In the worst case, a pipe wall may become progressively thinner over time until the pressure causes it to break open – hot hydrocarbons that are perhaps higher than the auto-ignition temperature can escape and mix with air, resulting in a potentially serious safety and environmental incident.
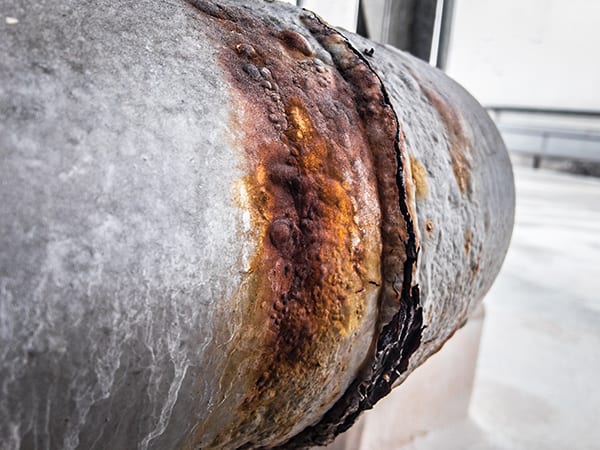
FIGURE 1. Unique corrosion issues can arise when petroleum refiners swap feedstocks
This is an extreme case, but not without precedent in the global petroleum refining industry. Opportunity crudes present unique challenges and they often have vastly different characteristics than the crudes many petroleum refineries are designed to handle. The feedstock may be more or less corrosive than the last batch, or corrosive in a different way, meaning that the corrosion risk to the inside of the process equipment is varying continuously.
For plant operators, corrosiveness has to be viewed as another process variable – it has to be measured and managed. However, in the past, there was little instrumentation available to characterize it and measure the impact that the corrosiveness of the process fluids has on process equipment. Fortunately, this situation is improving with the advent of more advanced corrosion-monitoring technologies, including wireless systems.
Corrosion is a very complex characteristic
The interaction of chemicals and metals has been studied extensively, and the mechanisms of corrosion-based metal loss and weakening are very complex. Countless articles and books have been written on the topic, but for this discussion, and to most operators in the real world, the question is straightforward: Is this process fluid eating away at my plant's pipe walls, and if so, at what rate?
The answer depends on the nature of the corrosive components of the process fluid, the operating parameters, such as flowrate or temperature, and the metallurgy of the pipe and vessel walls. Obviously, the metallurgy is fixed for all practical purposes, but in most facilities, it is not consistent across different areas and process units. There can be a variety of alloys used in different areas that have been installed at different times, and in varying states of health, with respect to pipe thickness.
Plant operators can work at forestalling the effects of corrosion in a variety of ways, including the following:
- Employing a corrosion allowance that recognizes the inevitability of metal loss and compensates by simply using thicker pipe sections in strategic areas.
- Establishing safe operating windows to slow the deterioration process. For example, operators may have concluded that metal loss with a specific grade of crude oil increases significantly beyond a specific temperature, so the process is adjusted to remain below the threshold. Obviously, this requires a great deal of knowledge about the characteristics of the crude and its interaction with the alloys, and it assumes the process will still work effectively at the adjusted parameters. Typically, the integrity operating window is set using theoretical concepts, which do not necessarily reflect reality.
- Material upgrades are a very effective approach. Replacing carbon-steel pipe with an appropriate stainless grade can extend its life, but it is very costly and cannot be done easily while a unit is running. If the next turnaround is not for another several years, a different approach will be necessary.
- Corrosion inhibitors can be quite helpful, but again, these have to be matched with the characteristics of the process fluid and the metallurgy to be effective. The additive designed for the crude or process fluid being handled currently might not work with what is slated for next week. It also adds cost, potentially offsetting the reason for running the opportunity crude in the first place.
- Inspections make sense, and can warn of impending problems if carried out correctly. However, they can be difficult to perform, since the operator must access specific points. Checking an elbow where there is no catwalk near the top of a tower that is clad in insulation is not an easy task. Moreover, manual inspections using a handheld ultrasonic measuring device do not have very high repeatability – remaining within±1 mm is doing well in most facilities. Furthermore, the need to access each location every time a measurement is desired means that, in practice, measurements are only taken every few years, which is not frequent enough to detect major corrosion events in many cases.
There is one strategy that can help make all of these activities more effective, and it begins with treating corrosion as a process variable and making the best use of corrosion data.
Measuring and monitoring metal loss due to corrosion
Process units in a petroleum refinery typically have hundreds and even thousands of process instruments measuring temperature, flow, pressure, level and other attributes. Operators can watch the readings in real time, and these readings are usually recorded in a historian system, so it is possible to see what a specific value was at a specific time in the past. This is valuable information in trying to figure out the causes of upsets and improving overall efficiency. Corrosion, quantified as actual metal loss measured in mils (one mil is equal to 1/1,000 of an inch) or micrometers (µm), can be treated the same way.
Wireless wall-thickness measurement sensors (Figure 2) can be installed throughout a unit on pipe and vessel walls to monitor metal thickness continuously. Data from these sensors can be transmitted over a wireless network to automation systems and process historians. Engineers can use these data to make decisions in real time, and the data can also be historized (Figure 3), just like data from a temperature or pressure transmitter or sensor, and retrieved for analysis.
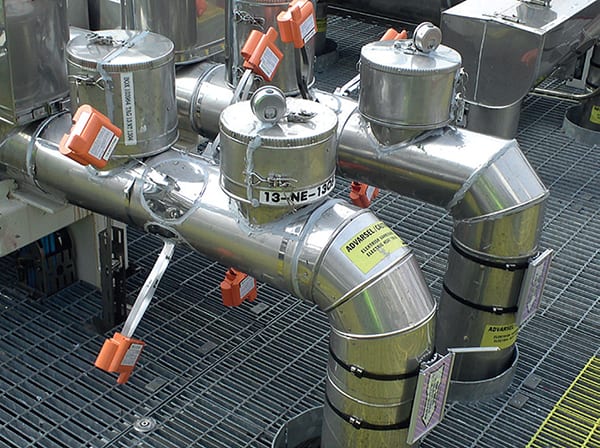
FIGURE 2. Non-intrusive wireless sensors monitor pipe wall thickness in real time and send data to the plant automation system via a wireless mesh network
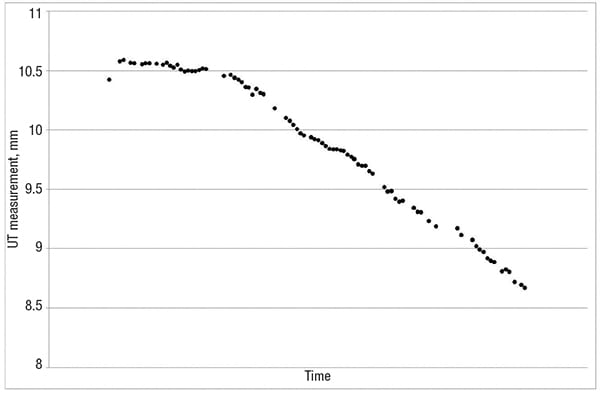
FIGURE 3. Ultrasonic-thickness (UT) measurement data can be collected and historized for analysis, just like any other process variable
Just as a pressure transmitter can warn when the equipment has exceeded a safe value, a thickness monitor can trigger an alarm when wall thickness has reached a safety threshold. This is an important function, but the ability to watch metal loss over time can provide even deeper insight into the process, and assist with other corrosion-mitigation strategies.
The variability of metal loss
With years of data collected using continuous wall-thickness monitoring in many facilities, one point has emerged time and again: metal loss is not a linear process. Experience has shown how it is common to see 80% of the metal loss during 20% of the time, or even 90% in 10% of the time. This accelerated metal loss happens when the corrosive elements really dig into the metal due to the presence of particularly aggressive corrosive elements that are unaffected by the inhibitors in use.
Metal loss is not a fast process, so observing it requires time and precision. Permanently mounted wireless ultrasonic-thickness sensors can achieve a repeatability of 10µm, which is the equivalent of 0.000394 in., so it is possible to detect very small changes over time. It is also possible to identify the variability in the rate of loss, a major improvement as compared to infrequent periodic inspections.
A hypothetical example. A well-trained inspector has taken two readings, one year apart, at exactly the same place with a handheld ultrasonic thickness-measuring device. Assuming that the device has a higher degree of accuracy than is likely possible in real life, the readings show a 1-mm reduction of wall thickness over that time period, indicating fairly aggressive corrosion. The conclusion based on two data points will suggest a more-or-less straight-line change (Figure 4) over the year. Looking at the same measurement point logged with a continuous monitor will far more likely show a jagged curve (Figure 5), where there are periods of rapid loss interspersed with times of very little change.
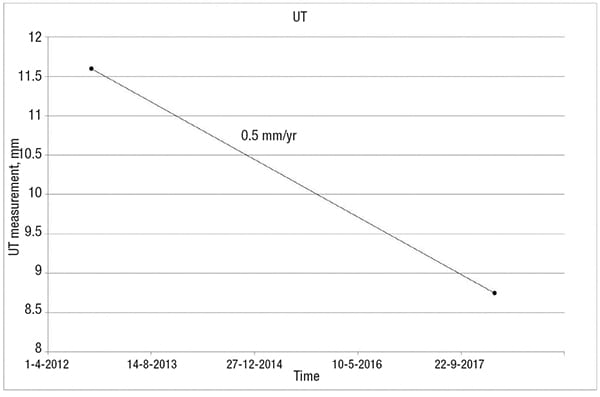
FIGURE 4. When wall-thickness measurements are made manually, there are often too few data points to provide useful statistical analysis
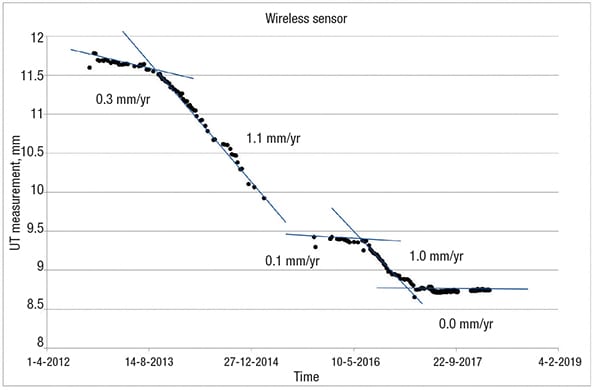
FIGURE 5. When wall-thickness data points are provided continuously, it becomes clear that metal loss is not a
linear process
Corrosion happens at highly variable rates because there are so many variable factors at play. Some of the factors are controlled – for example, the injection rate of a corrosion inhibitor or the operating temperature of a reactor – and others are not, such as the specific corrosion profiles that are brought into the process by the feedstock.
Trying to diagnose and solve the problem when there are very few data points is effectively impossible. Intrusive corrosion probes capable of giving an indication of the corrosiveness of the fluid and test coupons have their value, but they do not, on their own, deliver the most important measurement: actual metal loss, or lack thereof, in real time.
A case in point
The corrosion picture for a petroleum refinery is hugely complex, and some facilities may run as many as 50 different crude sources and grades throughout a year. But using data from wall-thickness monitors to identify potential cause-and-effect relationships between other process variables and periods of aggressive metal loss can help to maximize production capabilities and reduce losses. In some situations, the loss results from an especially corrosive crude, but there are also situations where process changes or upsets have unleashed an especially destructive period (Figure 6). These can be spotted by analyzing the continuous thickness data, and these findings are examined by determining what else was happening during that time. Did a process variable change? Was the wrong corrosion inhibitor used, or were no inhibitors used when they should have been? Are there any other factors to examine?
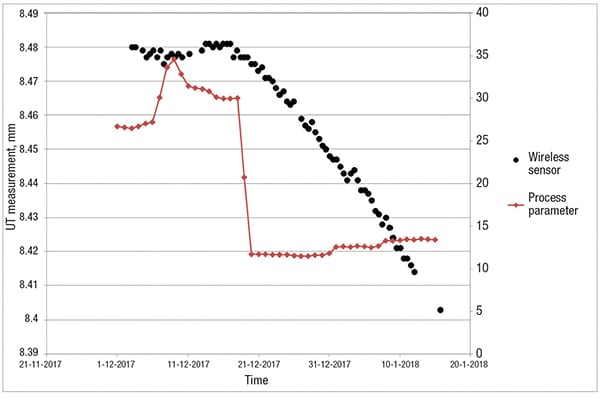
FIGURE 6. Process monitoring revealed the connection between a specific process condition and highly aggressive metal loss, allowing for rapid corrective action
The analysis shown in Figure 6 was used for review with a chemical company providing corrosion inhibitors to a petroleum refinery, and in this case, it was found that the formulation in use the previous week did not work as well with the particular crude running that day at the facility. Using corrosion measurement data, it was possible to fine-tune the selection process to improve formulations, matching additives with conditions.
Real-world lessons learned
Continuous metal-thickness corrosion monitoring, whether deployed sparsely to understand the overall corrosion picture, or in higher densities to understand the exact corrosion nuances of a specific area of the plant, supports the corrosion-mitigation strategies mentioned earlier. Data from the wireless sensors analyzed over time can determine the parameters of safe integrity operating windows and indicate the effectiveness of corrosion inhibitors. All of these elements work together to measure and mitigate this complex problem, regardless of the crude feedstock characteristics. Ultimately, knowing the current integrity of the plant, and how it is coping with the ever-changing corrosion burden, means that the facility can be driven to its maximum operating capability. ■
Edited by Mary Page Bailey
Author
Jake Davies is the marketing director for Rosemount corrosion monitoring systems at Emerson Automation Solutions, formerly known as Permasense Ltd. (Alexandra House, Newton Rd. RH10 9TT, Crawley, U.K.; +44 7884 317014; jake.davies@emerson.com). He has been involved in the development, deployment and support of non-intrusive wireless corrosion and erosion monitoring systems since 2008. Davies holds a doctorate from Imperial College London, a Masters of Engineering from Oxford University and an M.B.A. from The Open University.